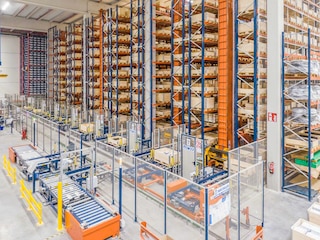
Jak wybrać najlepszy magazyn zautomatyzowany?
Magazyny zautomatyzowane to obiekty logistyczne, w których znaczna część operacji jest wykonywana w sposób automatyczny przy użyciu takich urządzeń transportu bliskiego jak układnice, przenośniki czy systemy transportu szynowego.
W zglobalizowanym świecie zorientowanym na najnowsze trendy, np. logistykę 4.0, firmy stanęły przed koniecznością obniżania kosztów operacyjnych i optymalizacji zarządzania towarem w celu uzyskania przewagi nad konkurencją. Wiele z nich, chcąc ograniczyć ryzyko błędów i zwiększyć swoją wydajność, stawia na automatyzację procesów magazynowych.
W niniejszym artykule przeanalizujemy korzyści płynące z automatyzacji magazynu. Zastanowimy się też, jakie aspekty należy wziąć pod uwagę przed podjęciem decyzji o zainwestowaniu w automatyczne urządzenia transportu bliskiego, aby unowocześnić i usprawnić łańcuch dostaw.
Zalety magazynów zautomatyzowanych
Magazyny zautomatyzowane pozwalają zoptymalizować i usprawnić procesy przyjęcia, składowania, kompletacji i wysyłki wszelkiego rodzaju produktów. Wiele firm wybiera to rozwiązanie ze względu na następujące korzyści:
- Wydajność i wysoka dyspozycyjność. Automatyzacja zapewnia ciągły i niezakłócony przepływ ładunków, ponieważ urządzenia transportu bliskiego mogą pracować 24/7.
- Mniejsze koszty zatrudnienia. Obsługa ładunków odbywa się bez udziału personelu. Pozwala to oddelegować operatorów i pracowników administracji do zadań o większym znaczeniu dla firmy.
- Ograniczenie kosztów serwisowych. Automatyczne przemieszczanie ładunków zmniejsza tempo zużywania się urządzeń transportu bliskiego oraz ryzyko ich niewłaściwego użytkowania.
- Bezpieczeństwo personelu. Magazyny automatyczne są zaprojektowane tak, aby ograniczyć obecność pracowników w obrębie instalacji. Dzięki temu operatorzy są mniej narażeni na zagrożenia, a ich stanowiska pracy mogą być bardziej ergonomiczne.
- Bezpieczeństwo ładunków. Brak bezpośredniego dostępu do ładunków chroni je przed zniszczeniem czy zgubieniem, pozwalając zachować każdy produkt w idealnym stanie.
- Inwentaryzacja w czasie rzeczywistym. Każdy magazyn automatyczny posiada system WMS zarządzający pracą obiektu, który śledzi i kontroluje stan magazynowy w czasie rzeczywistym. Możliwość rejestrowania ruchu ładunków umożliwia ścisłą identyfikowalność każdego produktu.
- Optymalne wykorzystanie przestrzeni. Rozwiązanie to zapewnia optymalną pojemność magazynową poprzez efektywne wykorzystanie dostępnej powierzchni. Magazyny automatyczne z łatwością dostosowują się do każdego budynku. Dodatkowo są skalowalne, co oznacza, że w razie potrzeby można je rozbudować.
Przed przystąpieniem do realizacji inwestycji należy skonsultować się z kompetentnym dostawcą tego rodzaju systemów. Powinien on przeanalizować potrzeby firmy oraz uwarunkowania jej instalacji logistycznej, aby dobrać najlepsze, spersonalizowane rozwiązanie. Mecalux to firma z wieloletnim doświadczeniem w dziedzinie magazynów zautomatyzowanych.
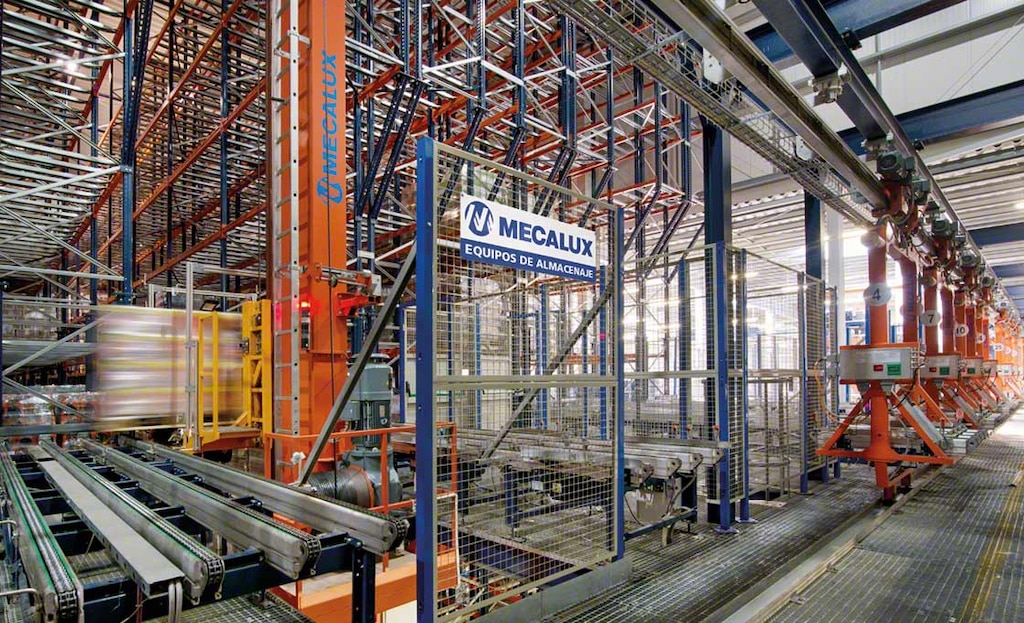
System transportu szynowego zapewnia bezpieczne przemieszczanie ładunków w magazynach zautomatyzowanych
Przed zaprojektowaniem magazynu automatycznego
Przed przystąpieniem do projektowania magazynu zautomatyzowanego należy przede wszystkim przeanalizować cele, jakie wyznaczyła sobie firma, jej potrzeby, oczekiwania w zakresie usprawnień oraz perspektywy jej dalszego rozwoju.
Możliwa jest automatyzacja istniejącego magazynu poprzez zastąpienie tradycyjnych rozwiązań systemami automatycznymi (transport ładunków za pomocą układnic i przenośników zamiast pracy operatorów) lub budowa magazynu automatycznego od zera.
Automatyzacja istniejącego obiektu logistycznego jest uwarunkowana dostępną przestrzenią, układem magazynu oraz wykonywanymi w nim operacjami. Natomiast druga opcja dopuszcza możliwość budowy instalacji automatycznej jako magazynu samonośnego, co pozwala wykorzystać całą dostępną przestrzeń, uzyskując większą pojemność magazynową.
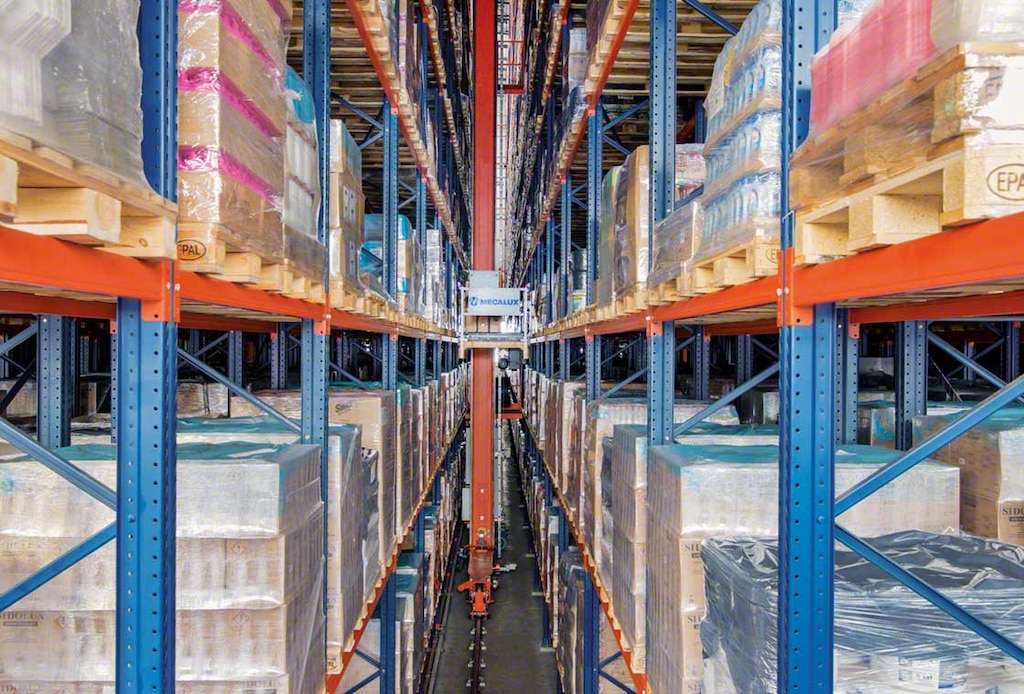
Układnice pobierają i odkładają ładunki w sposób automatyczny
Bez względu na wybrane rozwiązanie na początku należy rozpatrzeć kilka kluczowych aspektów dla działalności firmy:
Magazynowane ładunki
To podstawowy składnik aktywów każdej firmy, dlatego wymaga szczegółowej analizy:
- Nośniki ładunków, na których składowane będą produkty (palety lub pojemniki).
- Wymiary i waga produktów.
- Liczba składowanych produktów.
- Liczba jednostek asortymentowych oraz ich właściwości.
- Charakterystyka ładunków (wytrzymałość, wrażliwość na ogień, wilgoć itp.).
- Poziom popytu i wskaźnik rotacji.
Na podstawie tych danych można wybrać najlepszy system składowania oraz określić wymiary miejsc paletowych do przechowywania ładunków. System ten powinien poznać kierownik magazynu, aby dowiedzieć się, w jaki sposób będą wykonywane czynności magazynowe, a także, jakie strefy robocze powinien udostępnić.
Przestrzeń
W przypadku projektowania automatycznej instalacji magazynowej do istniejącego budynku należy dokładnie przestudiować główne cechy jego konstrukcji:
- Kształt budynku i jego wymiary.
- Charakterystykę architektoniczną oraz ograniczenia w postaci otworów (drzwi, okna) filarów itp.
- Charakterystykę i wytrzymałość posadzki.
- Normę budowlaną obowiązującą na danym terenie.
- Obliczenia sejsmiczne.
Dzięki tym informacjom dostawca systemów składowania może zaprojektować regały o właściwej wytrzymałości, które pozwolą wykorzystać dostępną przestrzeń tak, aby uzyskać jak największą pojemność magazynową.
Regały i urządzenia przeładunkowe
Analizując zaplecze logistyczno-magazynowe, powinniśmy rozważyć następujące zagadnienia:
- Wymiary regałów, ich liczbę oraz pojemność.
- Charakterystykę urządzeń transportu bliskiego, jakie będą stosowane w magazynie, m.in. maksymalną wysokość podnoszenia oraz udźwig.
- Możliwość wyposażania magazynu w nowe urządzenia.
Tego rodzaju dane służą do określania konieczności wprowadzania do magazynu nowych instalacji, do analizy ewentualnych ograniczeń konstrukcyjnych oraz możliwości zwiększenia pojemności magazynowej.
Przepływy i rotacja
Aspekt ten dotyczy rozmiaru i rozmieszczenia stref roboczych w obiekcie logistycznym, a także przyjętego sposobu wykonywania poszczególnych czynności magazynowych takich jak:
- Przyjęcia do magazynu (częstotliwość i wolumen).
- Transport ładunków.
- Kompletacja zamówień (wydajność i liczba linii dla każdego zamówienia).
- Wydania z magazynu (sposób sortowania zamówień, ich liczba i częstotliwość).
Na podstawie analizy powyższych danych możemy wybrać najbardziej odpowiedni system składowania: automatyczny lub obsługiwany ręcznie. Użytkownicy magazynów charakteryzujących się wysokim poziomem przepływu towaru decydują się zazwyczaj na rozwiązania automatyczne ze względu na bardzo wysokie tempo obsługi ładunków możliwe dzięki zastosowaniu układnic i przenośników. Z kolei firmy o mniejszych przepływach ładunków skłaniają się ku rozwiązaniom nieautomatycznym.
Nie istnieje żadna odgórna reguła określająca, jaki system magazynowy najlepiej odpowiada potrzebom danej firmy. Optymalne rozwiązanie musi być zawsze dostosowane do konkretnego przypadku i spełniać wszystkie indywidualne wymagania.
Systemy składowania w magazynach zautomatyzowanych
Analiza funkcjonalności poszczególnych systemów magazynowych to właściwy punkt wyjścia poprzedzający wybór najlepszego rozwiązania. Na początku podzielimy automatyczne systemy magazynowe na dwie grupy: regały z bezpośrednim dostępem (zapewniające łatwy dostęp do wszystkich ładunków) oraz regały akumulacyjne (efektywne wykorzystanie przestrzeni poprzez zagęszczenie ładunków na regale). Warto podkreślić, że systemy te mogą stanowić dwa uzupełniające się rozwiązania magazynowe.
Regały z bezpośrednim dostępem do ładunków
Magazyn można w prosty sposób zautomatyzować poprzez kombinację regałów paletowych o pojedynczej i podwójnej głębokości składowania oraz układnic paletowych trójstronnych. Zaletą tego typu urządzeń jest możliwość wdrożenia ich w każdym magazynie, w którym pracują wózki systemowe trójstronne obsługiwane przez operatorów. Układnice te cechuje łatwość zastosowania w istniejących magazynach, ponieważ nie wymagają dokonywania zmian w konstrukcji regałów, a także możliwość szybkiego zwrotu z inwestycji.

Układnice paletowe trójstronne w każdym magazynie mogą zastąpić trójstronne wózki systemowe obsługiwane przez operatorów
W przypadku budowy magazynu zautomatyzowanego od zera najczęściej wybieranym rozwiązaniem są układnice paletowe (nie trójstronne). Urządzenia te idealnie sprawdzają się w wysokich obiektach logistycznych (produkowany przez Mecalux model MT-5 osiąga nawet 45 m wysokości). Dzięki nim możliwe jest optymalne wykorzystanie całej dostępnej przestrzeni magazynu.
Systemy składowania akumulacyjnego
Systemy składowania akumulacyjnego to bloki regałów, które umożliwiają efektywne zagospodarowanie powierzchni magazynu i uzyskanie maksymalnej pojemności. Ceną takiego rozwiązania jest brak bezpośredniego dostępu do części ładunków. Przeważnie w magazynach obsługiwanych ręcznie stosuje się następujące systemy akumulacyjne: regały wjezdne, regały przepływowe, regały push-back oraz system Pallet Shuttle.
Z wymienionych powyżej rozwiązań pełnej automatyzacji można poddać jedynie regały przepływowe oraz system Pallet Shuttle. W pierwszym przypadku proces ten polega na montażu układnicy odpowiedzialnej za pobieranie, odkładanie oraz transport ładunków. Natomiast w automatycznym systemie Pallet Shuttle samojezdny wózek może być obsługiwany przez układnicę lub wózki wahadłowe.
W porównaniu z magazynami paletowymi automatyczne systemy składowania akumulacyjnego pozwalają znacznie efektywniej wykorzystać dostępną przestrzeń, oferując o wiele większą pojemność magazynu. Umożliwiają też szybsze tempo przepływu ładunków. Z drugiej strony nie są to rozwiązania zalecane do magazynów o dużej liczbie różnych jednostek asortymentowych.
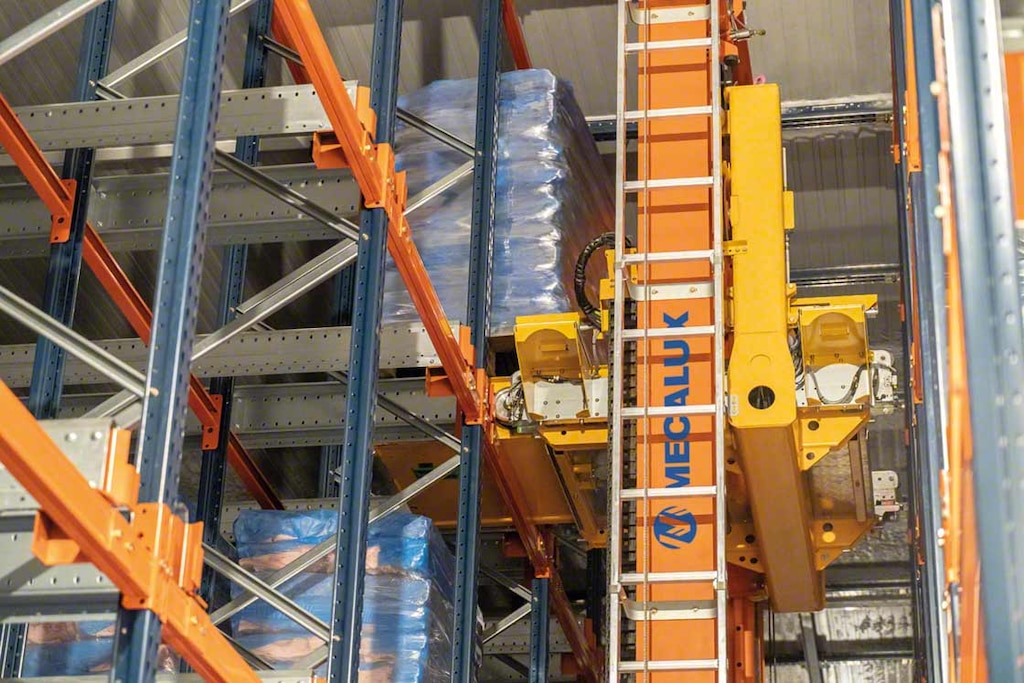
System Pallet Shuttle z układnicą usprawnia przepływ ładunków w magazynie
W kierunku magazynu zautomatyzowanego
Jeżeli myślisz o automatyzacji Twojego magazynu, skontaktuj się z ekspertami, którzy doradzą Ci optymalne rozwiązanie i przeprowadzą Cię przez proces planowania i wdrażania systemów automatycznych.
Mecalux ma wieloletnie doświadczenie w projektowaniu i uruchamianiu magazynów zautomatyzowanych dla firm ze wszystkich sektorów. Przykładem jednej z licznych realizacji jest magazyn automatyczny producenta elementów indukcyjnych SMA Magnetics w Zabierzowie koło Krakowa. Obiekt ten został wyposażony w układnice paletowe trójstronne odpowiedzialne za obsługę ładunków.
W obliczu dynamicznie zmieniającego się rynku wiele firm decyduje się na automatyzację, aby dostosować się do oczekiwań klientów i przyspieszyć swój dalszy rozwój. Jedną z nich jest brazylijskie przedsiębiorstwo logistyczne Iceport. Aby umocnić pozycję firmy na rynku Ameryki Łacińskiej, gdzie od kilka lat Iceport notował wzrosty sprzedaży, Mecalux wybudował samonośną automatyczną mroźnię o bardzo dużej pojemności, w której ładunki są przechowywane w kontrolowanej temperaturze -28ºC.
Rozmiar magazynu, liczba obsługiwanych palet, zmiany robocze oraz szeroko pojęte wymagania firmy to kluczowe czynniki, jakie mają wpływ na projekt magazynu zautomatyzowanego. Skontaktuj się z nami, a doradzimy Ci rozwiązanie skrojone na miarę Twoich potrzeb.