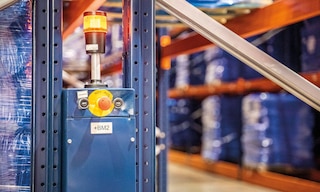
Jidoka – metoda poprawy procesów produkcyjnych
Jidoka jest jednym z narzędzi służących do utrzymania przepływu pracy i rozwiązywania problemów występujących w ramach lean supply chain.
Jidoka – co to jest i do czego służy?
Jidoka to podejście oparte na filozofii produkcji lean, która kładzie nacisk na kontrolę jakości na każdym kroku procesu produkcyjnego. Polega na zatrzymaniu linii produkcyjnych natychmiast po wykryciu błędu. Dzięki temu zapobiega wyprodukowaniu dużych ilości produktów wadliwych lub niespełniających standardów, zmniejsza możliwy negatywny wpływ na sprzedaż lub doświadczenie klienta, a także dąży do osiągnięcia efektywności operacyjnej.
Cel metody jidoka
Celem wdrożenia metody jidoka jest wytwarzanie produktów, które nie tylko spełniają wymagania użytkowników, ale także je przekraczają. Zatrzymanie linii produkcyjnej po pierwszej oznace problemu umożliwia rozwiązanie go bezpośrednio u źródła, zapobiega jego ponownemu wystąpieniu i sprzyja kulturze nastawionej na ciągłe doskonalenie.
Powstanie metody jidoka
Sakichi Toyoda, późniejszy założyciel grupy Toyota, zaprojektował krosna, które automatycznie zatrzymywały się za każdym razem, gdy zrywała się nić. Ten problem powodował wady w produktach, jednak urządzenie stworzone przez Toyodę powiadamiało o nim operatorów za pomocą sygnału wizualnego. Dzięki temu ograniczono przestoje w produkcji, a system zyskał samokontrolę.
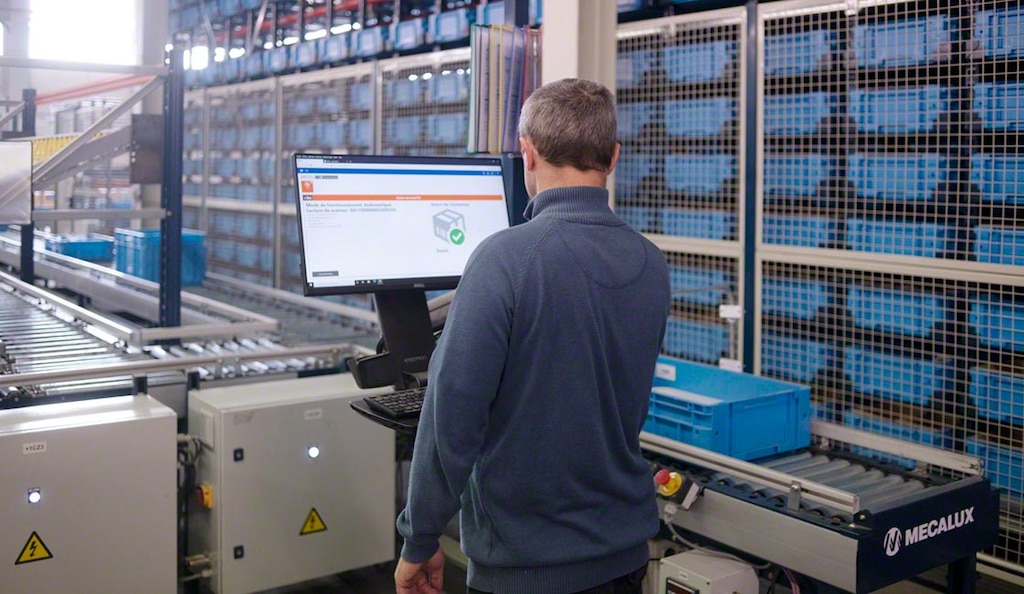
4 główne założenia metody jidoka
Metoda jidoka opiera się na czterech głównych założeniach, które ciągle są aktualne. Współcześni producenci mogą wdrożyć je, aby zapewnić ciągłość przepływów pracy i utrzymać takt time:
- Wykrycie błędu. Celem tej metody jest to, by maszyny były w stanie samodzielnie reagować na błędy i powiadamiać o nich pracowników, aby zapobiec zakłócaniu procesów. Omawiane podejście obejmuje wszelkiego rodzaju komplikacje, włącznie z wadliwymi produktami lub surowcami w złym stanie.
- Zatrzymanie produkcji. Po zidentyfikowaniu problemu urządzenia wstrzymują działanie bez interwencji człowieka. Jednak pracownicy również powinni mieć możliwość zatrzymywania linii w razie awarii.
- Podjęcie środków. Po szybkim rozwiązaniu problemu należy podjąć decyzję, czy możliwe jest wznowienie procesu produkcyjnego.
- Zapobieganie ponownemu wystąpieniu problemu. Jeśli problem został rozwiązany, osoba lub zespół odpowiedzialny za proces powinien przeanalizować powód jego wystąpienia, znaleźć sposoby zapobiegania ponownemu wystąpieniu problemu w długiej perspektywie i wdrożyć niezbędne ulepszenia, aby sytuacja się nie powtórzyła.
Jidoka i poka-yoke – różnice
Jidoka oraz poka-yoke to dwie techniki opracowane przez Toyotę, które pomimo wielu podobieństw oferują różne rozwiązania.
- Główną osią metody jidoka są urządzenia lub systemy, które samodzielnie wyłączają się po wystąpieniu problemu. W tym celu wykorzystuje się elementy monitorujące jak czujniki lub detektory. Dlatego metoda ta znana jest również jako autonomizacja, neologizm stanowiący połączenie idei autonomii i automatyzacji.
- Z kolei poka-yoke dąży do wyeliminowania wszystkich błędów poprzez wdrożenie środków zapobiegawczych. Jest skoncentrowana na powtarzających się czynnościach, przy których stosunkowo łatwo można popełnić błąd, i zapobieganiu ich występowaniu za pomocą przeznaczonych do tego urządzeń. Przykładem tego są mechanizmy bezpieczeństwa urządzeń AGD takich jak pralki, zmywarki czy kuchenki mikrofalowe, które nie dopuszczają do ich uruchomienia, zanim zostaną zamknięte.
Wdrożenie metody jidoka
Wdrożenie metody jidoka w firmie oznacza zmianę paradygmatu. Przyjęcie tej filozofii zakłada skupienie się na pozornie niewielkich komplikacjach i niemarginalizowanie ich podczas zajmowania się innymi pilnymi sprawami i terminami dostaw. Chociaż jidoka skupia się na maszynach, to na ludziach spoczywa obowiązek usprawnienia procesów. Poniżej omawiamy trzy pierwsze kroki wdrożenia metody jidoka:
- Współpraca z kadrą kierowniczą. Aby pomyślnie wdrożyć metodę jidoka, kadra kierownicza koniecznie musi poznać jej zalety i mieć świadomość, że tymczasowe wstrzymanie produkcji może okazać się szansą na rozwój. Dzięki temu cała firma będzie znała korzyści płynące z zastosowania strategii jidoka i nada jej taki sam priorytet jak innym systemom, np. just-in-time.
- Ocena sytuacji. Przed rozpoczęciem działań należy zastanowić się nad efektywnością procesów oraz nad skutkami i wymogami związanymi ze wdrożeniem metody jidoka.
- Rozpoczęcie od małych projektów. Zaleca się rozpoczęcie testów na kilku maszynach przed rozszerzeniem tej metody pracy na pozostałe obszary firmy.
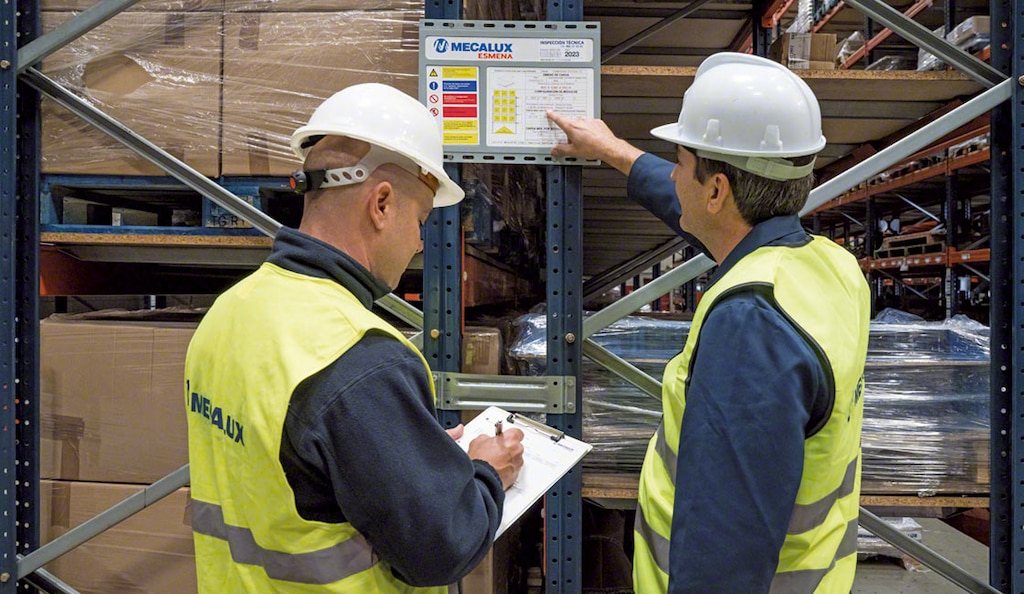
Zalety metody jidoka
Wdrożenie metody jidoka do realizacji operacji przynosi firmom, które stosują tę filozofię, wiele korzyści:
- Większa wydajność. Wczesne zidentyfikowanie nieprawidłowości zapobiega konieczności wstrzymywania i ponownego uruchamiania serii. Ponadto metoda ta pozwala operatorom pracować na więcej niż jednym urządzeniu jednocześnie.
- Mniejsze koszty. Zatrzymanie produkcji wadliwych produktów przekłada się na mniejsze koszty związane z naprawami, kapitałem ludzkim i zasobami.
- Zadowolenie klientów. Jakość produktów i terminowa realizacja dostaw poprawiają doświadczenie zakupowe klientów.
Przykłady zastosowania metody jidoka w codziennych sytuacjach
Poza krosnami w firmie Sakichiego Toyody jidoka ma zastosowanie również w codziennych przedmiotów i procesów:
- Urządzenia elektroniczne. Przykładem zastosowania metody jidoka w drukarkach domowych lub biurowych jest funkcja automatycznego zatrzymania drukowania w przypadku zacięcia papieru. Po zatrzymaniu drukowania urządzenia generują komunikat wizualny lub dźwiękowy, aby użytkownik ponownie włożył arkusze papieru do podajnika, zapobiegając marnowaniu tuszu lub narastaniu problemu.
- Transport. Pojazdy wyposażone są w kontrolki ostrzegawcze, które powiadamiają kierowcę o możliwej awarii.
- Opieka zdrowotna. Pracownicy służby zdrowia monitorują stan pacjentów poprzez monitorowanie ich parametrów życiowych. Po wykryciu jakiejś anomalii urządzenia powiadamiają personel medyczny, aby podjął natychmiastowe działania.
Od produkcji po logistykę
Najbardziej konkurencyjne firmy uważnie analizują swoje operacje, szukają sposobów na doskonalenie procesów i wdrażają najnowsze osiągnięcia technologiczne w celu usprawnienia pracy swoich zespołów. Automatyzacja magazynów i ich kontrolowanie za pomocą systemu zarządzającego Easy WMS Mecaluxu, zapewniająca dostęp do informacji i możliwość monitorowania produktów i poziomu zapasów, sprzyja osiągnięciu tego celu. Systemy te pozwalają na szybkie wykrycie anomalii, co spełnia pierwszy warunek metodologii jidoka. Skontaktuj się z nami – znajdziemy optymalne rozwiązanie dla Twojej firmy.