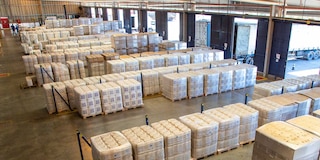
Jak obliczyć optymalną wielkość zamówienia w magazynie?
Utrzymanie optymalnego poziomu zapasów w magazynie ma kluczowe znaczenie dla zapewnienia efektywnej obsługi logistycznej, unikając nadmiernych kosztów magazynowania. Jaka jest odpowiednia liczba ładunków, aby sprostać popytowi, a przy tym uniknąć problemu braku zapasów w magazynie?
W niniejszym artykule analizujemy optymalną wielkość zamówienia w logistyce, omawiamy, czym różni się od zapasu minimalnego i zabezpieczającego, a także podajemy wzór umożliwiający obliczenie poziomu zapasów stosownie do zapotrzebowania, wielkości obiektu i tempa rozwoju firmy.
Definicja optymalnej wielkości zamówienia
Koncepcja optymalnej wielkości zamówienia określa dokładną ilość zapasów potrzebnych, aby zaspokoić standardowe zapotrzebowanie, zapobiegając brakom zapasów w magazynie. Jej celem jest uzyskanie maksymalnej rentowności przy jednoczesnym ograniczeniu do minimum kosztów magazynowania.
Nie należy mylić tej koncepcji z pojęciem średnich zapasów, czyli uśrednionego poziomu stanu magazynowego. Liczba ta oscyluje wokół zapasu maksymalnego, czyli łącznej liczby artykułów możliwych do składowania w obiekcie przy uwzględnieniu jego powierzchni i wykorzystywanych systemów magazynowych oraz punktu zamawiania lub zapasu minimalnego, czyli progu wskazującego konieczność uzupełnienia zapasów.
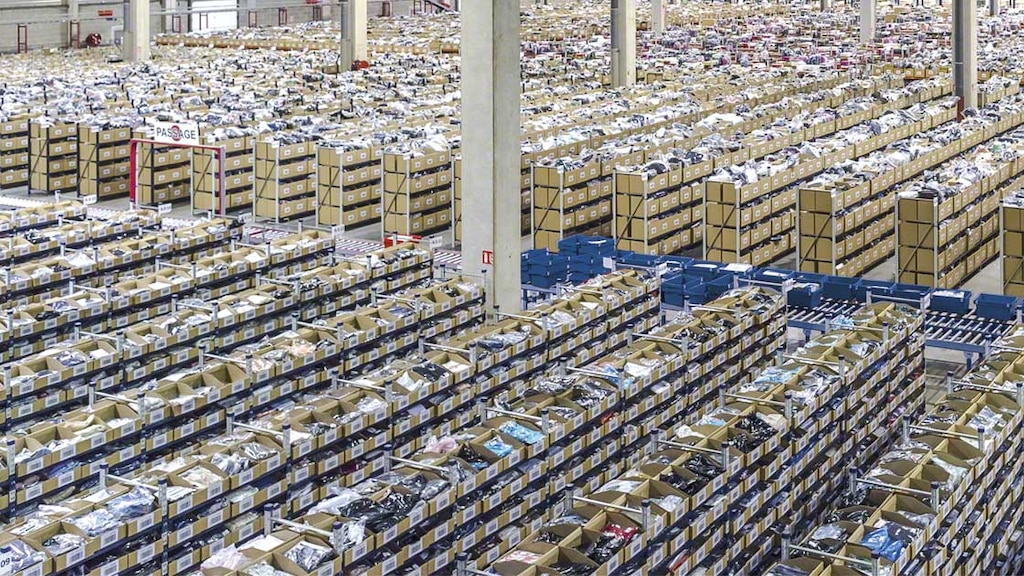
Lekceważenie konieczności określenia optymalnej wielkości zamówienia może prowadzić do poważnych konsekwencji w magazynie
Jak określić optymalną wielkość zamówienia w magazynie
Jakie czynniki powinien uwzględnić kierownik magazynu, aby określić optymalną wielkość zamówienia? Choć kwestia ta zależy od strategii obranej przez firmę, przedstawiamy cztery najważniejsze aspekty, które należy wziąć pod uwagę:
- Zapotrzebowanie ze strony klienta. Należy przeanalizować, we współpracy z działem księgowości i zarządzania, rozwój zapotrzebowania na przestrzeni lat, prognozy w odniesieniu do poszczególnych pozycji asortymentowych, ich sezonowość itp.
- Rotacja zapasów. Należy znać wskaźnik rotacji każdej pozycji asortymentowej, aby odpowiednio zarządzać rozmieszczeniem towaru. Do porządkowania zapasów stosownie do zapotrzebowania często wykorzystuje się analizę ABC.
- Rodzaj produktu. Właściwości produktów, jak również sektora działalności firmy, mają nadrzędne znaczenie podczas oceny optymalnej wielkości zamówienia przy uwzględnieniu zainstalowanych systemów magazynowych. Przykładowo, logistyka sektora spożywczego wymagająca magazynowania artykułów w warunkach chłodniczych ze względu na możliwość zepsucia towaru różni się od sposobu magazynowania okablowania czy rur, które to produkty wymagają określonych systemów magazynowych przystosowanych do ich specyfiki.
- Zapas maksymalny, zapas minimalny i zapas zabezpieczający. Mając wartości liczbowe tych trzech zmiennych, można obliczyć optymalną wielkość zamówienia dla każdej referencji (SKU). W związku z tym dostępna przestrzeń, metoda pracy, systemy magazynowe i urządzenia manipulacyjne determinują wielkość zapasu maksymalnego, a zapotrzebowanie oraz zdolność obsługi poszczególnych zamówień decydują o wielkości zapasu minimalnego. Z kolei charakterystyka prowadzonej działalności określa zapas zabezpieczający, niezbędny w każdym obiekcie.
- Czas realizacji. Kierownik magazynu powinien również znać lead time zapewniany przez poszczególnych dostawców. Oznacza to czas oczekiwania od momentu złożenia zamówienia na towar w magazynie po doręczenie produktu przez dostawcę.
W logistyce, w której coraz większą rolę odgrywa efektywność i możliwość ograniczenia kosztów magazynowania, lekceważenie konieczności określenia optymalnej wielkości zamówienia może pociągać za sobą pewne konsekwencje dla firmy, jak na przykład nieefektywne procesy magazynowe, ponoszenie kosztów gromadzenia nadmiernego zapasu towarów lub, przede wszystkim, pogorszenie jakości przechowywanych zapasów, szczególnie w przypadku szybko psujących się produktów.
Rodzaje zapasów: optymalny, minimalny, zabezpieczający
Nie sposób rozpatrywać optymalną wielkość zamówienia bez uprzedniego zrozumienia pojęć takich jak zapas bieżący, zapas zabezpieczający czy punkt zamawiania. Przyjrzyjmy się poszczególnym rodzajom zapasów stosownie do obranej strategii logistycznej:
- Zapas bieżący: ilość zapasów zgromadzonych w magazynie i wykorzystywanych do kompletacji dowolnego zamówienia. Na podstawie dostępnych zapasów prowadzone są wszystkie procesy logistyczne.
- Zapas minimalny: minimalna ilość każdego produktu, jaka powinna znajdować się w magazynie, aby pokryć zapotrzebowanie.
- Zapas zabezpieczający: każdy obiekt powinien posiadać zapas zabezpieczający (rezerwowy) w celu uniknięcia braku towaru w magazynie w przypadku nieoczekiwanego wzrostu popytu.
- Punkt zamawiania: wartość liczbowa określona w ramach strategii logistycznej wskazująca właściwy moment złożenia zamówienia u dostawcy. Plasuje się pomiędzy zapasem minimalnym i optymalnym.
- Zapas maksymalny: górna granica stanu magazynowego, której nie należy przekraczać w celu zapewnienia prawidłowego funkcjonowania obiektu. Szacowana jest w oparciu o dostępną pojemność oraz liczbę pracowników w magazynie.
Mając na uwadze powyższe kwestie, możemy obliczyć optymalny poziom zapasów w magazynie, czyli liczbę zapasów utrzymywanych w celu zagwarantowania maksymalnej rentowności firmy i sprostania zarówno obecnemu zapotrzebowaniu, jak i ewentualnym zmiennym tendencjom w przyszłości.
Wzór na optymalną wielkości zamówienia
Po uwzględnieniu wszystkich aspektów wymienionych powyżej należy zastosować wzór służący do obliczania optymalnej wielkości zamówienia. W celu określenia niezbędnych ilości poszczególnych artykułów w obiekcie, tzw. optymalnego poziomu zapasów, do uzyskanego wyniku należy dodać zapas minimalny i zapas zabezpieczający wymagany w magazynie. Poniżej objaśniamy, jak uzyskać te zmienne.
Optymalna wielkość zamówienia jest związana z formułą Wilsona, która na podstawie liczby i częstości składania zamówień u dostawców umożliwia osiągnięcie optymalnego zarządzania zapasami i zakupem surowców. W celu obliczenia tej wielkości należy zastosować następujący wzór:

Wzór wyrażający optymalną wielkość zamówienia bazuje na formule Wilsona
Gdzie Q oznacza optymalną wielkość zamówienia, D roczne zapotrzebowanie na rozpatrywany surowiec, K stanowi koszt każdego zamówienia, a G koszt magazynowania produktu przez określony czas. W ten sposób za pomocą formuły Wilsona można określić moment złożenia każdego kolejnego zamówienia.
Oprócz optymalnej wielkości zamówienia należy określić zapas minimalny oraz zapas zabezpieczający. Aby określić zapas minimalny w magazynie, należy zastosować następujący wzór:

Wzór umożliwiający obliczenie zapasu minimalnego
Do tej wartości należy doliczyć zapas zabezpieczający, obliczany na podstawie następujących zmiennych:
- Czas realizacji dostawy przez dostawców w standardowych okolicznościach (SLT).
- Maksymalny czas trwania procesu zaopatrzenia w przypadku wystąpienia niesprzyjających okoliczności (MPLT).
- Średni popyt na produkt (APD).

Wzór umożliwiający obliczenie zapasu zabezpieczającego
Wreszcie wzór pozwalający na obliczenie zapasu optymalnego wygląda następująco:
Zapas optymalny = optymalna wielkość zamówienia + zapas minimalny + zapas zabezpieczający
Przykładowe obliczenia
Przeanalizujmy powyższe wzory na konkretnym przykładzie. Firma z sektora obróbki metali posiada magazyn surowców zaopatrujący zakład produkcyjny w śruby. Firma potrzebuje 80 000 śrub rocznie w celu wytworzenia płyt metalowych przeznaczonych do sprzedaży.
Każde zamówienie składane przez firmę u dostawcy śrub stanowi koszt rzędu 100 euro, a koszt składowania jednej śruby wynosi 5 centów w skali roku. Jaki optymalny poziom zapasów śrub powinien znajdować się w magazynie firmy?
Jak wspomnieliśmy, pierwszym krokiem podczas wyznaczania optymalnego poziomu zapasów jest obliczenie optymalnej wielkości zamówienia. Na podstawie wzoru, gdzie K (koszt każdego zamówienia) wynosi 100 €, D (roczne zapotrzebowanie) wynosi 80 000 śrub, a G (koszt jednostkowy składowania jednej śruby) wynosi 0,05 €, uzyskujemy wartość Q wynoszącą 17 888 śrub.
Q czyli optymalna wielkość zamówienia = √((2 x 100 x 80 000) / 0,05) = 17 888 śrub
Następnie, aby obliczyć optymalny poziom zapasów, należy określić zapas minimalny potrzebny w magazynie. W tym celu należy ustalić zapotrzebowanie firmy na śruby w przeliczeniu na jednostkę czasu (dzień). Jeżeli przyjmiemy, że firma prowadzi działalność przez 250 dni w roku, okazuje się, że potrzebuje 320 sztuk dziennie. W związku z tym, skoro czas realizacji dostawy przez dostawcę wynosi tydzień, niezbędny zapas minimalny wynosi 2240 sztuk.
Zapas minimalny = (80 000 / 250) x 7 = 320 x 7 = 2240 śrub
Na koniec obliczamy zapas zabezpieczający, który należy zapewnić w magazynie. Jeżeli maksymalny czas realizacji dostawy przez dostawcę w nietypowych okolicznościach wynosi 21 dni, to zapas zabezpieczający powinien wynosić 4480 sztuk.
Zapas zabezpieczający = (21 - 7) x 320 = 4480 śrub
Oznacza to, że optymalny poziom zapasów wynosi 24 608 śrub, jako suma optymalnej wielkości zamówienia (17 888), zapasu minimalnego (2240) i zapasu zabezpieczającego (4480).
Optymalny poziom zapasów = 17 888 + 2240 + 4480 = 24 608 śrub
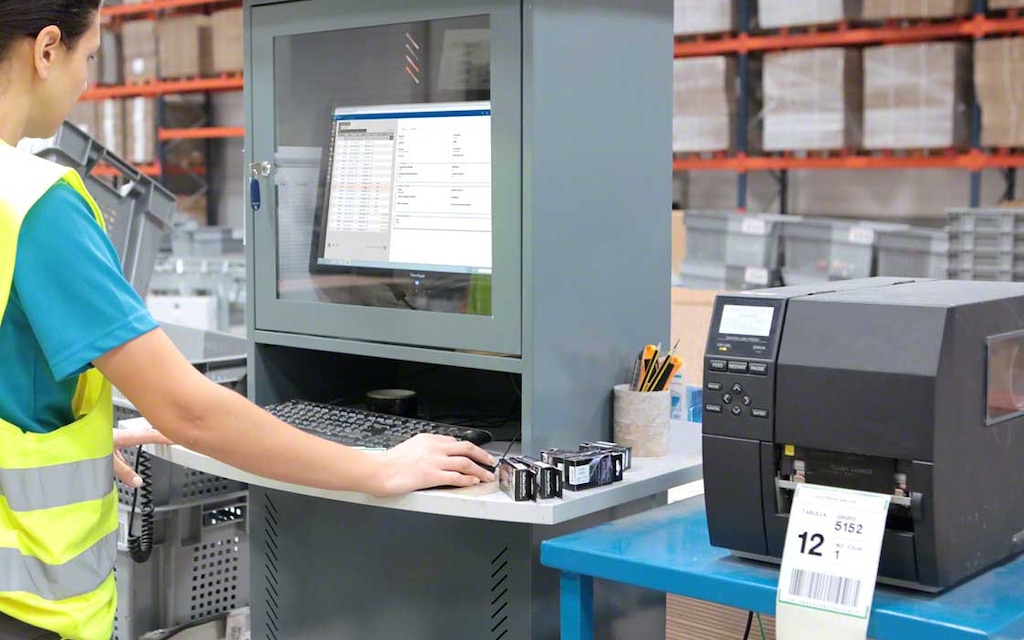
System WMS automatycznie zarządza takimi czynnościami, jak kompletacja zamówień czy uzupełnianie zapasów
Cyfryzacja optymalnej wielkości zamówienia
Cyfryzacja procesów logistycznych umożliwia zautomatyzowanie wielu czynności, które dotąd były powodem błędów i wymagały większych nakładów pracy operatorów. Dzięki wdrożeniu systemu ERP (Enterprise Resources Program) możliwe jest zintegrowane zarządzanie zamówieniami w magazynie, zyskując m.in. informacje o zapotrzebowaniu na poszczególne produkty oraz czasie realizacji dostaw przez poszczególnych dostawców. Wdrożenie właściwego oprogramowania pomaga w obliczaniu optymalnego poziomu zapasów oraz optymalnej wielkości zamówień składanych u każdego dostawcy.
Po obliczeniu optymalnej ilości dla poszczególnych pozycji magazynowych, system zarządzania magazynem (WMS) może automatycznie wyznaczyć priorytety w zakresie takich procesów, jak uzupełnianie zapasów w strefach kompletacji, odbiór zamówień przychodzących do magazynu, a nawet zarządzanie liniami produkcyjnymi w obiekcie.
Ponadto tego rodzaju oprogramowanie pozwala na określenie optymalnej wielkości zamówienia w odniesieniu do każdej pozycji asortymentowej, aby automatycznie tworzyć zlecenia uzupełnienia zapasów w przypadku przekroczenia ustalonej wartości granicznej. W odniesieniu do składowania towaru w magazynie, system WMS automatycznie przypisuje lokalizację produktom stosownie do ich właściwości (rotacja produktu, partia lub termin przydatności), ograniczając liczbę błędów i zwiększając wydajność instalacji.
Precyzja i elastyczność jako clou logistyki 4.0
W świetle coraz większych wymagań logistyki i przemysłu firmy są zmuszone do ograniczenia kosztów procesów magazynowania i kompletacji zamówień w celu utrzymania konkurencyjności. Z tego względu stosowanie takich rozwiązań, jak określanie optymalnej wielkości zamówienia, pozwala na wyeliminowanie błędów i nadmiernych kosztów. Gwarantuje to dostateczną ilość zapasów potrzebną, aby sprostać zapotrzebowaniu na poszczególne artykuły.
Tym niemniej, coraz częściej to właśnie kierownicy magazynów wdrażają rozwiązania umożliwiające automatyzację przepływu zapasów. Po obliczeniu optymalnego poziomu zapasów system WMS we współpracy z systemem ERP umożliwia zaplanowanie zamówień u dostawców, wyznaczenie kolejności uzupełniania zapasów w poszczególnych lokalizacjach oraz oferuje wiele innych zaawansowanych funkcji.
Firma Mecalux opracowała rozwiązanie w postaci systemu Easy WMS, który jest wyposażony w wiele funkcjonalności znajdujących zastosowanie w sektorze logistyki. Skontaktuj się z nami, jeśli chcesz usprawnić procesy w Twojej firmie oraz zyskać pełną kontrolę nad posiadanymi zapasami. Nasi konsultanci pomogą znaleźć rozwiązanie skrojone na miarę Twoich potrzeb.