
Pomieszczenia czyste (clean room) – jak pozbyć się zanieczyszczeń
Pomieszczenia czyste, zwane również sterylnymi lub typu clean room, są to obszary zaprojektowane specjalnie w celu utrzymania otoczenia w warunkach pozbawionych jakichkolwiek zanieczyszczeń. W przypadku niektórych produktów, zanieczyszczenia mogą wywierać negatywny wpływ na ich jakość, a nawet prowadzić do zakażeń, co może narazić na szwank reputację firmy, a w skrajnych przypadkach doprowadzić do poniesienia przez nią konsekwencji prawnych w przypadku spowodowania zagrożenia zdrowia konsumentów.
Z tej przyczyny pomieszczenia sterylne powinny znajdować się w części zakładów produkcyjnych, szczególnie z sektora farmaceutycznego, spożywczego i chemicznego. Clean rooms stanowią odpowiedź na konieczność usunięcia cząstek zawieszonych w powietrzu w celu uniknięcia zanieczyszczenia produktów. Wymogi i przepisy dotyczące późniejszej eksploatacji muszą być priorytetowymi wytycznymi branymi pod uwagę w trakcie ich projektowania i budowy. Dla utrzymania sterylnych warunków w trakcie użytkowania tych pomieszczeń zasadnicze znaczenie ma ich dokładne czyszczenie i odkażanie w regularnych odstępach czasu.
W niniejszym artykule zdefiniujemy pomieszczenia typu clean room, przedstawimy sposób ich projektowania, możliwe zastosowania oraz przebieg ich budowy w magazynie.
Definicja clean room
Clean room to czyste i jałowe pomieszczenie robocze, w którym poziom zanieczyszczeń (np. pył lub opary chemiczne), ciśnienie, temperatura, wilgotność i oświetlenie podlegają ścisłej kontroli w celu uniknięcia przekroczenia ich granicznych wartości określonych w obowiązujących przepisach. Wszelkie odbywające się w pomieszczeniach czynności i procesy przebiegają w warunkach bezpiecznych i wolnych od zanieczyszczeń.
Instalacje te należy budować i projektować w określony sposób, z uwzględnieniem odpowiedniego wyposażenia (układy wentylacyjne HEPA, prysznice powietrzne, śluzy powietrzne itp.). Do pomieszczenia typu clean room ma dostęp wyłącznie personel upoważniony do wykonania odpowiednich czynności bez narażania produktów na kontakt i działanie czynników mogących prowadzić do ich zanieczyszczenia.
Zastosowania pomieszczeń typu clean room
Idea pomieszczenia czystego pochodzi z medycyny, a konkretnie ze szpitalnych sal operacyjnych. W celu wykonania zabiegu chirurgicznego należy bezwzględnie zapewnić prawidłową temperaturę i wentylację pomieszczenia, sterylizację wykorzystywanych narzędzi i zgodność z surowymi wymogami higienicznymi.
W celu zagwarantowania bezpieczeństwa produktów wytwarzanych w niektórych branżach, koncepcję tę zaimplementowano w przemyśle, wszędzie tam, gdzie również konieczne jest zachowanie kontroli nad poziomem zanieczyszczeń. Dotyczy to szczególnie sektorów: spożywczego, medycznego, farmaceutycznego, technologicznego i innych.
Obecność drobnoustrojów w otoczeniu może mieć negatywny wpływ na właściwości niektórych produktów. Ma to szczególne znaczenie w przypadku produkcji i dystrybucji żywności. Każdy kontakt artykułów spożywczych (wyrobów mięsnych, ryb, nabiału, warzyw czy dań gotowych) z zanieczyszczeniem może powodować zagrożenie dla zdrowia, a nawet życia spożywających je ludzi.
Przepisy dotyczące clean room
Kontrola i minimalizacja poziomu zanieczyszczeń w pomieszczeniu czystym jest niełatwym zadaniem i wymaga bardzo precyzyjnego zaprojektowania takiej przestrzeni. Należy uwzględnić wiele aspektów: od specyfikacji technicznej warunkującej jej poprawne funkcjonowanie (tu kluczową rolę odgrywają filtry HEPA), przez przepisy regulujące proces budowy lub wymagane wyposażenie, po przewidywane natężenie przepływu personelu i rotacji ładunków.
Na etapie opracowywania projektu i jego wdrażania stosuje się dwie normy, których kryteria określają charakterystykę pomieszczenia czystego:
- GMP (Dobra Praktyka Produkcyjna, ang. Good Manufacturing Practice). Są to międzynarodowe przepisy regulujące produkcję leków, kosmetyków czy żywności w optymalnych warunkach otoczenia. W Europie ich stosowanie podlega postanowieniom rozporządzenia Parlamentu Europejskiego i Rady (WE) nr 1223/2009. W celu zapewnienia zgodności z przepisami należy nie tylko zadbać o czystość powietrza, ale również upewnić się, że clean room posiada odpowiednią regulację temperatury, właściwe oświetlenie i ochronę przeciwpożarową. Równocześnie należy zapewnić sterylność używanych materiałów i powierzchni, na których mają być wykonywane poszczególne czynności.
- ISO 14644. Jest to międzynarodowy standard opracowany przez Międzynarodową Organizację Normalizacyjną (ISO) w celu zagwarantowania higieny powietrza w pomieszczeniach typu clean room. Norma ta dzieli pomieszczenia na dziewięć kategorii, z określeniem maksymalnych wartości granicznych w odniesieniu do ilości cząstek wewnątrz. Podział ten może być bardziej lub mniej restrykcyjny w zależności od branży. Od zaledwie 0,2 mikrometra cząstek na metr sześcienny powietrza (lotnictwo, farmacja czy sektor szpitalny) po 293 tys. mikrometrów. Podstawowym celem budowy pomieszczeń czystych jest minimalizacja wytwarzania, utrzymywania i przenikania do nich cząstek zanieczyszczeń.
Projekt i budowa
Podczas projektowania pomieszczenia typu clean room należy opracować rozkład dostępnej przestrzeni, zadbać o jej wygrodzenie, zaprojektować drzwi, okna oraz posadzkę, a także przewidzieć sposób filtracji i punkty dostępu. Na tym etapie należy wziąć pod uwagę przeznaczenie pomieszczenia czystego oraz warunki zewnętrzne.
Materiały wykorzystywane do budowy powinny odznaczać się wyższą jakością niż te zastosowane do wszelkich innych budowli. Wynika to z konieczności spełnienia szeregu kryteriów: trwałości, odporności fizycznej i chemicznej, łatwości czyszczenia i zachowania w przypadku kontaktu z ogniem.
Norma ISO 14644 określa kilka wymogów dotyczących konstrukcji pomieszczenia czystego:
- Okładziny ścian i sufity. Powinny być wykonane z płyt warstwowych, czyli płyt złożonych z dwóch powierzchni zewnętrznych zwykle wykonanych z galwanizowanej blachy stalowej oraz wypełnienia zapewniającego sztywność całej konstrukcji (oraz dodatkowe właściwości, takie jak ognioodporność i odpowiedni poziom izolacji cieplnej). Dzięki właściwemu połączeniu płyt można zablokować przedostawanie się drobnoustrojów do wnętrza pomieszczenia i gromadzenie się w nim pyłu, a także ułatwić czyszczenie.
- Drzwi i okna. Drzwi również powinny być wykonane z warstwowych płyt izolacyjnych, a okna powinny posiadać podwójną szybę zabezpieczającą.
- Posadzki. Istnieje możliwość zastosowania różnych rodzajów wykończenia, w zależności od natężenia ruchu w pomieszczeniu. Optymalnie posadzki powinny być gładkie, aby uniknąć wnikania zabrudzeń, ułatwić czyszczenie i uniemożliwić namnażanie się drobnoustrojów.
- Oświetlenie. Należy stosować lampy fluorescencyjne o neutralnej barwie białej.
Kolejny etap projektowania cleen roomu polega na wyborze właściwych filtrów. Jest to jeden z najważniejszych elementów wyposażenia pomieszczeń tego typu. Powietrze wprowadzane do wnętrza hermetycznego pomieszczenia podlega filtracji w celu ograniczenia ilości zawieszonych cząstek stałych. Jest wymieniane kilka razy dziennie, aby uniemożliwić powstawanie pyłu. Za wymianę i jakość powietrza odpowiadają filtry HEPA wykonane z włókien szklanych wychwytujących i zatrzymujących cząstki zawieszone i drobnoustroje.
W celu zapewnienia prawidłowego przebiegu procesu produkcyjnego, odpowiednich warunków pracy oraz ograniczenia ryzyka zanieczyszczeń krzyżowych istotnym aspektem jest również klimatyzacja pomieszczeń.
Zalecane jest stworzenie śluzy powietrznej (ang. Security Airlock System, SAS), czyli komory wyposażonej w dwie kurtyny dostępowe (jedne do wnętrza pomieszczenia, drugie na zewnątrz), które nigdy nie są otwierane jednocześnie. System ten zapobiega gwałtownym zmianom temperatury i ciśnienia podczas dostępu do pomieszczenia czystego.
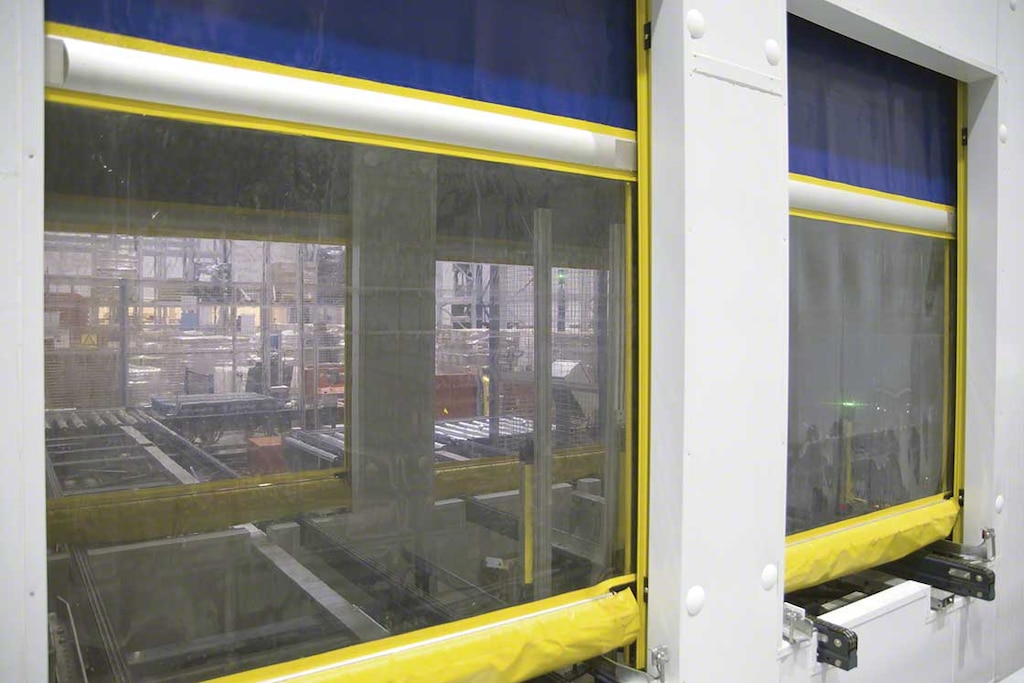
Utrzymanie sterylności pomieszczeń czystych
Bieżące utrzymanie w czystości clean roomu jest niezmiernie istotne dla utrzymania jego podstawowej funkcjonalności. Należy kontrolować higienę personelu oraz czystość materiałów wprowadzanych do pomieszczenia. W tym celu konieczne jest odpowiednie przeszkolenie i poinstruowanie operatorów w zakresie znaczenia kwestii czystości. Pracownicy powinni stosować specjalną odzież pochłaniającą zanieczyszczenia naturalnie wytwarzane przez skórę i ciało człowieka, a w niektórych przypadkach powinni również stosować siatki na włosy, rękawice oraz maseczki.
Punkty dostępu to kolejny ważny aspekt, ponieważ to właśnie tam istnieje zwiększone ryzyko wprowadzenia cząstek stałych i innych zanieczyszczeń do wnętrza pomieszczenia. Aby zminimalizować ryzyko, stosowane są prysznice powietrzne przeznaczone dla pracowników. Są to miejsca stworzone w celu pozbycia się zarazków z powierzchni ciała przed wejściem do pomieszczenia czystego.
Clean room w magazynie
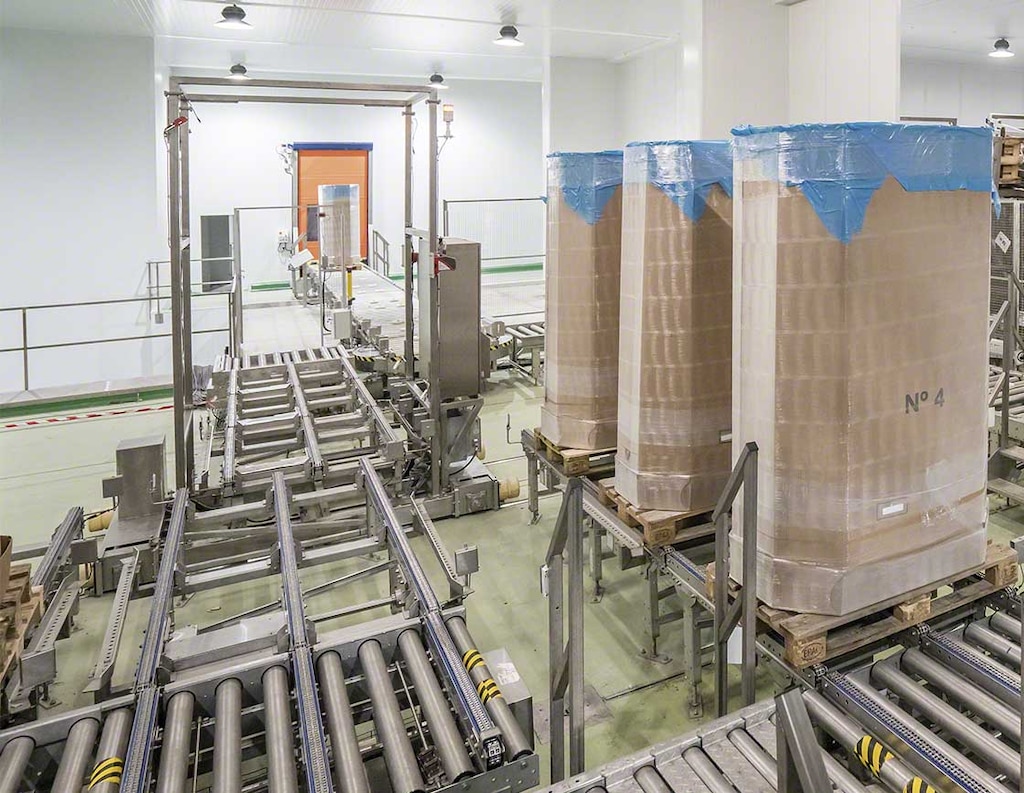
W logistyce koncepcja pomieszczenia czystego znajduje zastosowanie w mroźniach i chłodniach, a zatem w obiektach lub komorach izolowanych w celu zapobiegania przenikaniu energii cieplnej. Chłód jest jednym z najczęstszych rozwiązań stosowanych w celu konserwacji produktów (przede wszystkim żywności czy leków) przez wyznaczony okres czasu.
Aby zagwarantować właściwy poziom izolacji cieplnej obiektu, jego ściany, sufit, posadzki i drzwi muszą być wykonane z materiałów o odpowiednim poziomie izolacyjności termicznej i szczelności gazowej. Ponadto należy zadbać o instalację sprężarek i parowników w górnej części budynku. Nadrzędnym celem tego rozwiązania jest utrzymanie stabilnej temperatury w trakcie realizacji całego procesu logistycznego oraz wyeliminowanie punktów krytycznych, które mogłyby doprowadzić do przerwania łańcucha chłodniczego produktów.
Jednym z najlepszych rozwiązań w tym zakresie są magazyny samonośne pracujące w kontrolowanych warunkach termicznych. Ich konstrukcję nośną tworzą regały, do których mocowana jest okładzina ścian i dachu. Tego rodzaju obiekty zajmują wyłącznie niezbędną przestrzeń, umożliwiając maksymalizację pojemności magazynu. Jedną z głównych zalet tego rozwiązania jest ograniczenie kosztów zużycia energii związanej ze stałym utrzymywaniem niskiej temperatury w instalacji.
Pomieszczenia typu clean room w magazynach automatycznych
W logistyce chłodniczej coraz większą rolę odgrywa automatyzacja. Jest to rozwiązanie gwarantujące optymalną pojemność magazynową przy jednoczesnym zapewnieniu całkowitej kontroli nad warunkami obsługi ładunków. System przenośników i układnic umożliwia stały i bezpieczny przepływ towaru, skracając czas obsługi oraz eliminując ryzyko błędów związane z ręczną manipulacją ładunkami.
Oto najczęściej stosowane automatyczne systemy magazynowe i transportowe w mroźniach lub chłodniach:
- Przenośniki. Transportują ładunki automatycznie, zastępując urządzenia transportu bliskiego (wózki widłowe) obsługiwane przez operatorów. W mroźniach i chłodniach wykorzystuje się przenośniki wykonane ze stali nierdzewnej, z uwagi na ich wysoką odporność na korozję.
- Układnice. Przemieszczają ładunki w korytarzach obsługowych ze strefy wejścia do magazynu automatycznego do wyznaczonej lokalizacji na regałach, które mogą mieć pojedynczą lub podwójną głębokość składowania.
- System Pallet Shuttle. Czynności wykonywane w magazynie są w pełni zautomatyzowane dzięki zastosowaniu samojezdnego wózka, którego zadaniem jest pobieranie i umieszczanie ładunków na regałach. Jest to jeden z najbardziej efektywnych systemów ze względu na jego kompaktowy charakter. Rozwiązanie to umożliwia zwiększenie wydajności pracy dzięki zwiększeniu liczby obsługiwanych cykli.
- Wdrożenie systemu zarządzania magazynem (przykładowo Easy WMS firmy Mecalux), przyczynia się do zwiększenia wydajności magazynu automatycznego. Oprogramowanie pełni funkcję centrali zarządzającej wszystkimi elementami współpracującymi ze sobą w obiekcie logistycznym — od urządzeń przeładunkowych po czynności wykonywane w celu efektywnego zarządzania stanem magazynowym.
Kontrola, czystość i bezpieczeństwo
Przedsiębiorstwa z sektora spożywczego, farmaceutycznego czy chemicznego muszą stosować pomieszczenia typu clean room do bezpiecznej produkcji lub obróbki czy konfekcjonowania produktów. Pomieszczenia te są izolowane w celu zapewnienia czystości powietrza i uniknięcia przenikania zanieczyszczeń (np. pyłu zawieszonego czy drobnoustrojów) do ich wnętrza, ponieważ mogłoby to doprowadzić do pogorszenia jakość produktów.
W sektorze logistycznym całkowicie izolowanymi instalacjami są chłodnie, mroźnie i magazyny, w których konieczne jest utrzymanie ścisle kontrolowanej atmosfery. W tego rodzaju obiektach magazynowane są produkty, które wymagają przechowywania w precyzyjnie określonych warunkach. W związku z tym dla ich utrzymania, niezbędna jest właściwa izolacja tych magazynów.
Mecalux posiada wieloletnie doświadczenie w projektowaniu i budowie tego rodzaju obiektów dla przedsiębiorstw z sektora spożywczego, chemicznego i farmaceutycznego. Przyjrzyjmy się trzem przykładom wdrożeń:
- Bem Brasil. Ten producent mrożonych frytek wyposażył swoją mroźnię (-30 ºC) w automatyczny system Pallet Shuttle zapewniający pojemność magazynową przekraczającą 33 tys. palet. Firma zdecydowała się na wdrożenie tego akumulacyjnego systemu ze względu na możliwość szybkiej obsługi dużej liczby palet z tą samą pozycją asortymentową.
- Schaal Chocolatier. Ten wiodący producent czekoladek pochodzący z Francji posiada automatyczny magazyn o pojemności 6200 palet, składający się z pięciu korytarzy z regałami o pojedynczej głębokości składowania. Cztery z pięciu korytarzy pracują w temperaturze 14 ºC, natomiast piąty wymaga utrzymania temperatury 5 ºC. Na regałach składowane są wyroby gotowe, półprodukty, surowce, opakowania i wyposażenie niezbędne w każdym dniu pracy.
- Takeda. Koncern farmaceutyczny Takeda wybudował automatyczny magazyn samonośny o pojemności 6584 palet. Obiekt jest wyposażony w system kontroli temperatury i wilgotności powietrza, który utrzymuje temperaturę w przedziale 16 - 24 ºC i uniemożliwia przekroczenie 70% wilgotności. Ponadto w magazynie, jako zabezpieczenie przeciwpożarowe zastosowano system inertyzacji, polegający na obniżeniu zawartości tlenu w atmosferze w celu uniemożliwienia rozprzestrzeniania się ognia.
Jeżeli planujesz budowę pomieszczenia typu clean room w swoim magazynie lub myślisz o wdrożeniu zautomatyzowanego systemu w chłodni – skontaktuj się z nami. Przeanalizujemy Twoją sytuację i pomożemy Ci znaleźć najlepsze rozwiązanie.