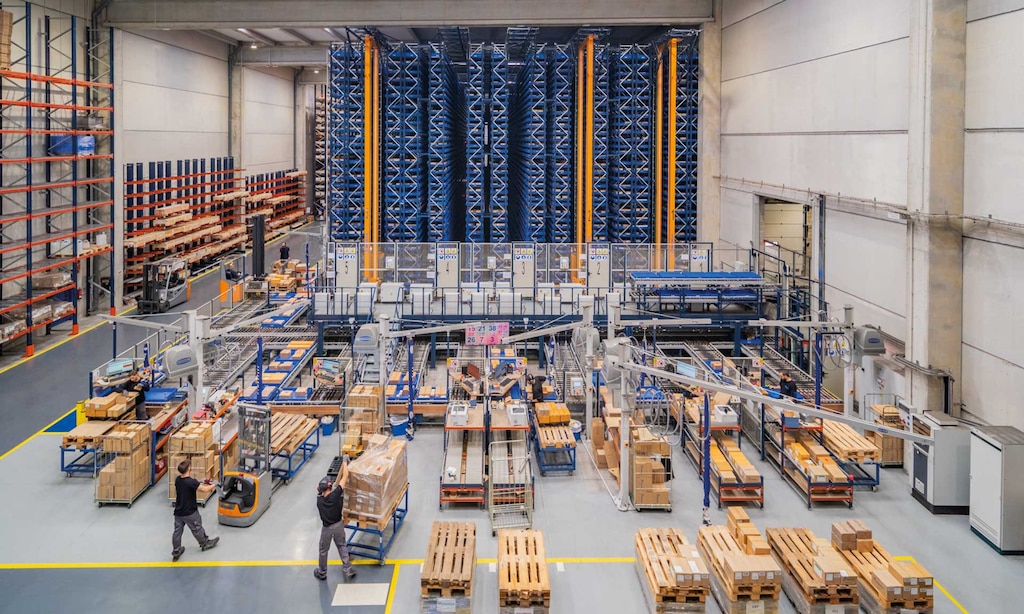
BADANIA LOGISTYCZNE
Diego Pacheco, Daniel Møller Clausen i Jendrik Bumann
Magazyny stanowią główny filar łańcucha dostaw, a od jego sprawnego funkcjonowania zależy w ogromnej mierze doświadczenie klienta. Jednakże kierownictwo tych obiektów każdego dnia mierzy się z licznymi wyzwaniami. Największe spośród nich to brak skutecznych kontroli jakości, nadmiarowe procesy, niewłaściwy układ magazynu oraz brak dokładnych informacji o zapasach. Jeżeli nie zostaną podjęte odpowiednie kroki, każda z tych kwestii może skutkować dodatkowymi kosztami, spadkiem wydajności i niezadowoleniem klientów.
W systemie produkcyjnym firmy Toyota działania, które nie przynoszą wartości dodanej, lecz stratę, określane są japońskim słowem muda, oznaczającym „marnotrawstwo”. Według tej filozofii istnieje siedem rodzajów marnotrawstwa, do których należą: oczekiwanie, nadprodukcja, podwójna obsługa towaru, zbędny transport, nieodpowiednie procesy, błędy i wady oraz nadmierne zapasy.
Świadomość aktualnej sytuacji w magazynie stanowi pierwszy krok do zidentyfikowania obszarów marnotrawstwa. Pomagają w tym m.in. analiza danych, obserwacja magazynu, wywiady i kwestionariusze, analiza Pareta oraz narzędzia stosowane w szczupłym zarządzaniu (ang. lean management), takie jak np. mapowanie strumienia wartości (ang. value-stream mapping – VSM) oraz genba shikumi, czyli narzędzie ilościowe oparte na wektorach i macierzach korelacji. Dla uzyskania wysokiej wydajności i przewagi konkurencyjnej przedsiębiorstwa niezbędne jest wdrożenie programów ciągłego doskonalenia.
Wąskie gardła w magazynie
W przeprowadzonym badaniu zostało poddane analizie funkcjonowanie magazynu dystrybucyjnego należącego do duńskiej firmy z sektora MŚP. Firma zajmuje się sprzedażą produktów w modelach B2B i B2C w całej Europie, a w magazynie zatrudnia kierownika na cały etat i pomocnika w niepełnym wymiarze godzin. Najpierw badacze opracowali strategie identyfikowania i minimalizowania marnotrawstwa w procesie magazynowym, a następnie zastosowali je w badanym przedsiębiorstwie.
Zespół badawczy zauważył, że kierownictwo firmy ma świadomość, iż pewne problemy operacyjne mają niekorzystny wpływ na jej wyniki. Brak proaktywnych działań w celu zaradzenia sytuacji może utrudniać skalowalność firmy na rynku.
Gromadzenie danych do analizy odbyło się w kilku etapach. Najpierw przeprowadzono wywiad z właścicielem, by poznać firmę, jej pracowników oraz magazyn. Następnie zebrano dalsze obserwacje w trakcie trzech wizyt. Posłużono się również kwestionariuszami w celu uzyskania informacji na temat dostaw towaru do magazynu oraz wysyłek zamówień do klientów, a także wykorzystano raporty sprzedaży i zapasów, aby określić, jakie zyski przynoszą poszczególne rodziny produktów.
Zidentyfikowanie nieodpowiednich procesów
Badacze dostrzegli, że istotny czynnik w procesie magazynowym stanowiła nawet pogoda: gdy nie było opadów, rozładunek i sortowanie dostarczonego towaru odbywały się na zewnątrz, gdzie jest więcej miejsca. Na etapie kompletacji zamówień, niekiedy problematyczne było znalezienie produktów. Wówczas pracownik kompletujący albo sam szukał produktu, albo prosił o pomoc kolegę, albo przekazywał zamówienie do wysyłki bez danego produktu. Podczas pakowania natomiast najważniejszym czynnikiem była dostępność odpowiednich kartonów i wypełniaczy. Jeżeli nie było ich pod ręką, operator musiał ich poszukać. Brakowało także systemu załadunku zamówień na ciężarówkę.
Firma wysyłała średnio 128 produktów dziennie jednym transportem. Co dwa miesiące od swojego głównego dostawcy otrzymywała 367 paczek zawierających 9715 produktów i chociaż komunikacja z nim odbywała się za pośrednictwem poczty elektronicznej, przepływ informacji w firmie był wciąż ręczny.
Brak metody umieszczania produktów w miejscach składowania powodował, że wiedzą o zapasach dysponował jedynie kierownik magazynu, co stanowiło dla firmy problem, jeśli był on przez dłuższy czas nieobecny
Magazyn miał tylko jednego pełnoetatowego pracownika, dlatego przy rozładunku dostaw musiał pomagać personel biurowy. Jeśli rozładunek trwał dłużej niż godzinę, firmie transportowej trzeba było dodatkowo zapłacić, natomiast brak odpowiedniego sprzętu powodował, że pracownicy byli narażeni na znaczny wysiłek fizyczny. Ponadto, ponieważ towar był załadowywany w sposób losowy, niemetodyczny, sortowano go dopiero po rozładowaniu, co zajmowało dodatkowy czas.
Brak metody umieszczania produktów w miejscach składowania powodował, że wiedzą o zapasach dysponował jedynie kierownik magazynu, co stanowiło dla firmy problem, jeśli był on przez dłuższy czas nieobecny. Personel biurowy pomagał w obsłudze magazynu, lecz nie był odpowiednio przeszkolony w tym zakresie, a także nie znał poziomów i lokalizacji zapasów, w związku z czym zadawał kierownikowi dużo pytań, utrudniając mu pracę.
Etap kompletacji rozpoczynał się z chwilą, gdy pracownik pobierał wydruk zamówienia, którego następnie używał jako listy kompletacyjnej. Jeśli personel biurowy umieścił wydruk z nowym zamówieniem na wierzchu zamiast włożyć pod spód, wówczas wcześniejsze zamówienie było realizowane później. Ponadto etykiety na pudełkach były małe i niewyraźne, więc trudno je było odczytać. Kartony układano jeden na drugim, co utrudniało ich przemieszczanie. Bez systemu zarządzania magazynem pracownicy polegali na własnej pamięci, aby znaleźć najszybsze trasy, w związku z czym personel tymczasowy miał jeszcze bardziej utrudnione zadanie.
Wyniki i mapa strumienia wartości
Wyniki pokazały, że większość czynności odbywających się w magazynie można usprawnić. Chociaż firma się rozwinęła, nie zmieniła sposobu pracy, co doprowadziło do licznych problemów, takich jak podwójna obsługa towaru (ang. double handling). Ponadto pracownicy nie otrzymują informacji zwrotnych na temat swojej pracy otrzymywanych od klientów i nie znają swoich błędów.
Badanie wykazało, że trzy główne rodzaje marnotrawstwa w tej firmie to oczekiwanie, podwójna obsługa towaru oraz zbędny transport wewnętrzny. Do obszarów wymagających pilnej uwagi, obok głównego procesu, należą także rozładunek i sortowanie towaru. W związku z tym zaproponowano szereg zmian mających na celu poprawę funkcjonowania magazynu. Zostały one przedstawione w postaci mapy strumienia wartości (rysunek).
Najbardziej znaczącą zmianą zaproponowaną w nowej mapie strumienia wartości było wdrożenie systemu zarządzania magazynem (ang. Warehouse Management System – WMS). Tego typu oprogramowanie usprawnia cały strumień wartości, ponieważ gromadzi wszystkie dane dotyczące każdego produktu i każdej czynności. Dzięki temu na przykład powiadamia o nadchodzących dostawach, umożliwiając pracownikom przygotowanie się zawczasu do przyjęcia towaru. Wyznacza miejsce składowania dla każdego produktu, zanim zostanie on dostarczony do magazynu, co sprawia, że odkładanie towaru przebiega szybciej. System WMS można ponadto połączyć z programami do kompletacji głosowej. Komunikaty ASN (ang. Advanced Shipping Notices) pozwalają również z wyprzedzeniem zlecić zadania związane z rozładunkiem i sortowaniem towaru.
Kolejnym wnioskiem z badań była potrzeba wprowadzenia standardowych procedur operacyjnych (ang. Standard Operating Procedures – SOP) dla dostawcy, procesu rozładunku i klasyfikacji oraz pakowania. Procedury te obejmują wymogi dotyczące wielkości i widoczności etykiet oraz sposobu układania towaru przed wysyłką.
Wdrożenie systemu zarządzania magazynem
System WMS może mieć pozytywny wpływ na wszystkie prace magazynowe, niezależnie od tego, czy będzie używany samodzielnie, czy też zostanie zintegrowany z systemem planowania zasobów przedsiębiorstwa (ERP). Oprogramowanie magazynowe pozwala skrócić oczekiwanie oraz wyeliminować podwójną obsługę i zbędny transport towaru. Dzięki prognozom sprzedaży można zaplanować z większą precyzją odpowiednie poziomy zapasów i zapobiec ubytkom magazynowym.
Tego rodzaju program może rozwiązać problemy w zakresie zarządzania miejscami składowania i proponować lokalizacje dla nowych jednostek asortymentowych zgodnie z metodą ABC. Dzięki jego wskazówkom optymalizacyjnym można wprowadzić udogodnienia: cięższe produkty umieszczać nieopodal stanowisk kompletacyjnych, a produkty sprzedawane zwykle razem składować blisko siebie. System może również działać jako narzędzie do planowania, monitorując, czy magazyn dysponuje wystarczającą liczbą kartonów o różnych rozmiarach, aby szybko i sprawnie zapakować zamówienia.
Wydajność magazynu wpływa na wiele obszarów, a usprawnienie procesu magazynowego przynosi korzyści we wszystkich aspektach działalności firmy
Identyfikowanie i analizowanie źródeł marnotrawstwa w magazynach sprawia, że pracownicy lepiej rozumieją znaczenie swojej pracy, to zaś zwiększa ich satysfakcję zawodową. Wyniki badań dowodzą, iż eliminowanie marnotrawstwa przekłada się na bardziej efektywne wykorzystanie zasobów, co sprzyja rozwojowi przedsiębiorstwa i stwarza nowe możliwości biznesowe.
Wydajność magazynu wpływa na wiele obszarów, a usprawnienie procesu magazynowego przynosi korzyści we wszystkich aspektach działalności firmy. Mapa strumienia wartości badanego magazynu wskazuje, że całkowity czas operacji wynosi 1721,29 godziny, natomiast po wdrożeniu systemu WMS oraz wprowadzeniu usprawnień we wszystkich operacjach mógłby zostać skrócony aż o 41,4%.
AUTORZY BADANIA:
Diego Pacheco, Daniel Møller Clausen i Jendrik Bumann, Katedra Technologii i Rozwoju Biznesu, Wydział Biznesu i Nauk Społecznych, Uniwersytet w Aarhus (Dania).
Publikacja w wersji oryginalnej:
Diego Augusto de Jesus Pacheco, Daniel Møller Clausen i Jendrik Bumann. A multi-method approach for reducing operational wastes in distribution warehouses, „International Journal of Production Economics”, 2023, 256.
© The Authors. Licensed under CC BY 4.0