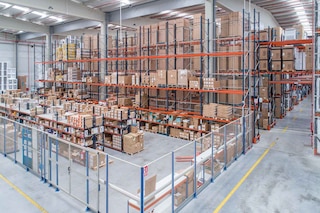
Jakie są kluczowe kryteria rozmieszczenia towarów w magazynie?
Zarządzanie procesem rozmieszczania towarów w magazynie polega na wyznaczeniu odpowiedniego miejsca do ich składowania, co ma na celu przyspieszenie czynności pobierania i zoptymalizowanie przepływu ładunków.
Sposób organizacji produktów w danej lokalizacji jest określany na podstawie szeregu kryteriów regulujących rozmieszczanie towarów w magazynie. Które z reguł stosuje się najczęściej? Jakie czynniki należy wziąć pod uwagę podczas ich doboru? W dalszej części artykułu szczegółowo odpowiemy na te pytania.
Najczęściej stosowane kryteria regulujące rozmieszczanie ładunków
Wyodrębniamy dwie podstawowe zasady lokalizacji:
- Stałe lub określone miejsce składowania towaru w magazynie: każdemu kodowi pozycji asortymentowej (SKU) z wyprzedzeniem przypisuje się konkretne położenie. Ułatwia to lokalizowanie produktów bez konieczności korzystania z informatycznego systemu rejestrującego ich usytuowanie.
- Metoda wolnych miejsc składowania: pozycje są umieszczane losowo w dostępnych miejscach paletowych. Skuteczna realizacja tej strategii wymaga korzystania z systemu zarządzania magazynem.
W wielu obiektach jest stosowana strategia mieszana łącząca obydwie wyżej wymienione zasady rozmieszczania towarów w magazynie.
Jak określić kryteria rozmieszczania towarów w magazynie?
Zastosowanie danej reguły lokalizacji asortymentu na regałach zależy przede wszystkim od trzech istotnych kwestii:
1. Analiza właściwości magazynowanych pozycji asortymentowych
- Właściwości fizyczne produktów: wymiary (długość, szerokość i wysokość) oraz ciężar artykułów mają kluczowe znaczenie przy doborze odpowiednich instalacji magazynowych oraz opracowywaniu optymalnego systemu obsługi ładunków. Przykładowo, najcięższe produkty powinny być składowane na najniższych poziomach regałów. Zaleca się także stosowanie ujednoliconej, najlepiej zautomatyzowanej metody obliczeń wymiarów produktów w celu uniknięcia rozbieżności. W związku z tym, aby uprościć proces pakowania zamówień, zwykle określa się standardowe wymiary opakowań, w których zmieści się każdy z magazynowanych artykułów.
- Pozostałe parametry i kryteria: zwykle uwzględnia się między innymi zgodność z innymi produktami składowanymi w obiekcie (magazynowanie substancji chemicznych podlega przepisom prawa), odporność na działanie warunków atmosferycznych (przechowywanie w magazynach otwartych może ograniczyć koszty eksploatacji) lub termin ważności szybko psujących się produktów (należy je uporządkować według dat i zadbać o odpowiednią temperaturę i poziom wilgotności, a także wskazać numer partii jako element umożliwiający identyfikowanie towaru).
2. Analiza dostępnych systemów magazynowych i organizacji przestrzeni w magazynie
- Ustalenie nomenklatury identyfikującej poszczególne lokalizacje w obiekcie: identyfikacja powinna uwzględniać aspekty przestrzenne, takie jak rodzaj magazynu, numer korytarza czy typ strefy. Szczegółowe i precyzyjne oznaczenia poszczególnych poziomów wysokości, miejsc paletowych oraz kanałów lub półek minimalizują ryzyko popełnienia błędów podczas pobierania towaru. Zastosowana nomenklatura może składać się z liter, numerów lub zbioru cyfr tworzących unikalny kod lokalizacji.
- Obliczenie pojemności i stopnia obłożenia magazynu: w przypadku przekroczenia 90-95% pojemności warto sprawdzić rozmieszczenie towarów w magazynie, aby ustalić, czy na pewno dostępna przestrzeń jest wykorzystywana w optymalny sposób. Należy przy tym uwzględnić również konkretny rodzaj regału — czy jest to system akumulacyjny, czy z bezpośrednim dostępem do towaru. Pierwszy wskazany jest dla magazynów, w których przechowuje się dużą liczbę palet z tym samym asortymentem, natomiast drugi ma bardziej wszechstronny charakter i wykorzystywany jest przy zarządzaniu niewielką liczbą palet przypadającą na każdy z produktów.
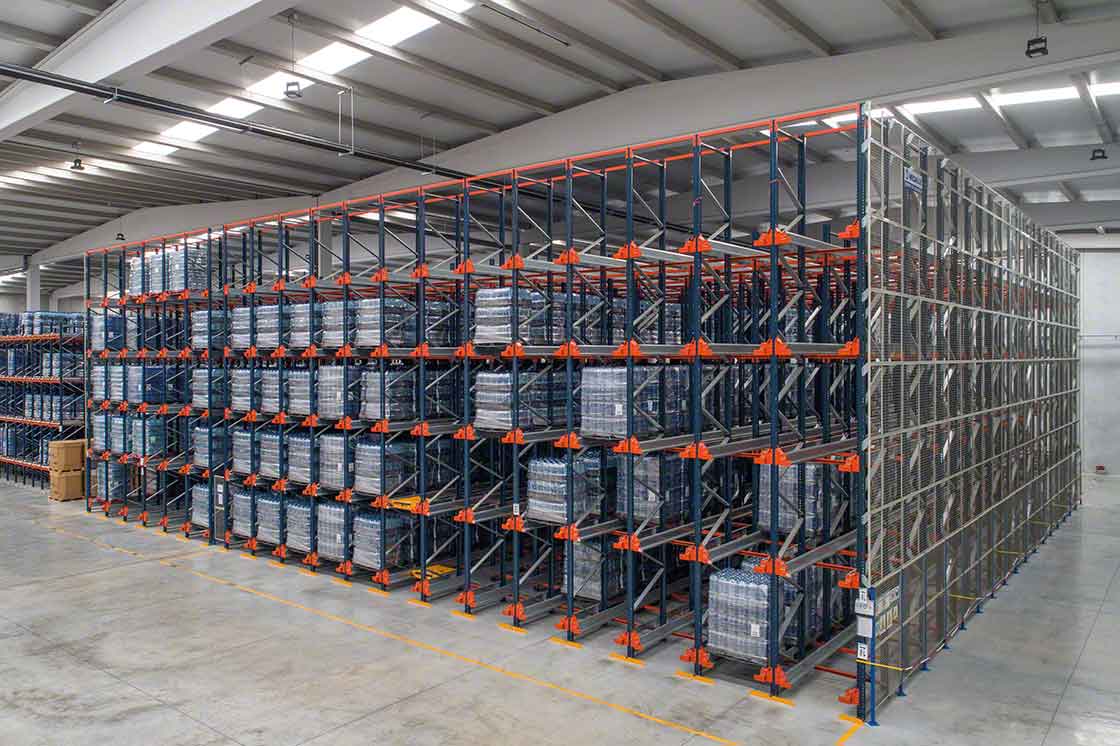
3. Analiza przepływu towarów i ruchu operatorów w obiekcie
- Przepływy towarów:
1. Wskaźnik rotacji zapasów: umożliwia uporządkowanie magazynowanych artykułów stosownie do częstotliwości, z jaką opuszczają magazyn. Obliczana jest na podstawie zapotrzebowania odnotowywanego na przestrzeni całego roku. W zależności od tempa rotacji produkty są przypisywane do jednej z grup: A,B lub C. Zgodnie z ogólnym kryterium regulującym rozmieszczanie towarów w magazynie produkty, na które popyt jest większy powinny znajdować się w pobliżu ramp załadunkowych, natomiast asortyment o niższym poziomie rotacji powinien być umieszczany w dalszych częściach obiektu.
2. Metoda zarządzania FIFO lub LIFO: dotyczy kolejności przepływu towarów. Zasada FIFO (First In, First Out) polega na wydawaniu w pierwszej kolejności produktów o najwcześniejszym terminie przydatności do spożycia. Z kolei według zasady LIFO (Last In, First Out) magazyn w pierwszej kolejności opuści towar, który trafił do niego jako ostatni.
- Ruch operatorów:
Dystans pokonywany przez każdego operatora zależy przede wszystkim od przyjętej metody kompletacji, dostępności produktów na regałach oraz stosowanych urządzeń transportu bliskiego i systemów automatycznych. Dla przykładu obiekty wyposażone w przenośniki i układnice ograniczają ręczną manipulacje towarem, eliminując tym samym konieczność częstego przemieszczania się.
Zarządzanie rozmieszczeniem towarów w magazynie ma na celu uzyskanie optymalnej pojemności magazynowej, zminimalizowanie czynności przeładunkowych oraz dostosowanie każdego miejsca składowania do właściwości produktów.
Przeprowadź gruntowną analizę reguł stosowanych w Twoim magazynie dzięki oprogramowaniu Easy WMS firmy Mecalux i zoptymalizuj gospodarkę zapasami. Skontaktuj się z nami, a pomożemy Ci opracować najwłaściwsze kryteria regulujące rozmieszczenie towarów w obiekcie.