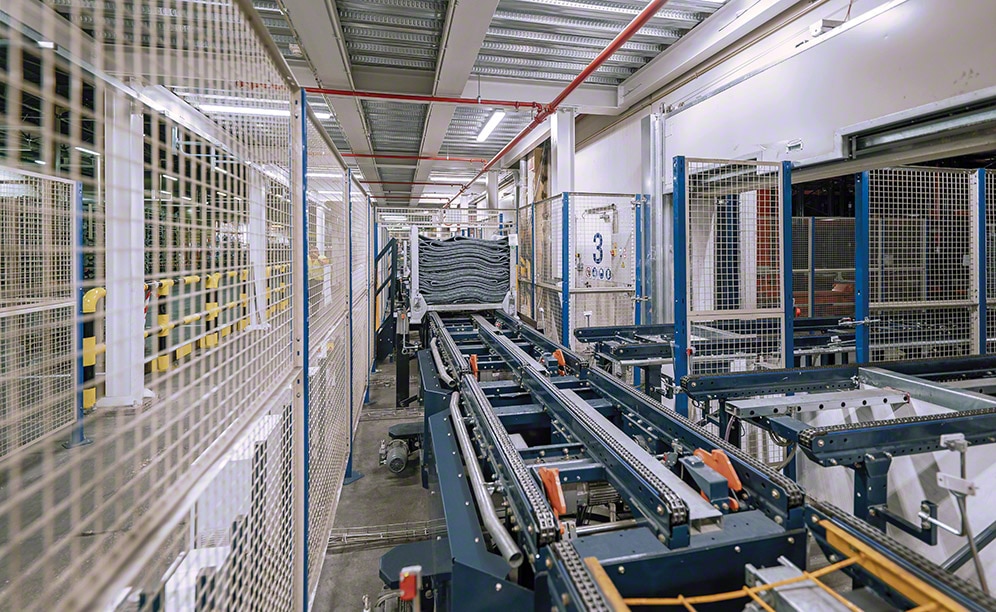
Automatyczny magazyn samonośny zintegrowany z fabryką opon Michelin w Vitorii
Michelin posiada w Vitorii w północnej części Hiszpanii jedną z największych w tym kraju fabryk opon
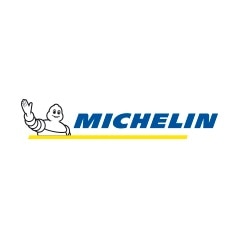
Zwiększenie produkcji będące konsekwencją notowanego w ostatnich latach wzrostu sprzedaży skłoniło firmę Michelin do rozbudowy fabryki w hiszpańskiej Vitorii. Mecalux potrzebował zaledwie 8 miesięcy, aby zbudować automatyczny magazyn samonośny w pełni gotowy do użytkowania i dostosowany do składowania jednostek ładunkowych wykorzystywanych przez producenta opon. Obiekt jest całkowicie zautomatyzowany – przenośniki, układnice, wózki wahadłowe i windy transportują towar według wytycznych, jakie Michelin przedstawił zespołowi technicznemu Mecaluxu.
Rozbudowa zakładu produkcyjnego
W 1889 roku we Francji bracia André y Édouard Michelin założyli przedsiębiorstwo, którego celem było opracowanie zaawansowanych rozwiązań dla transportu. Od tamtej pory aż do dziś misją firmy jest dążenie do poprawy mobilności ludzi i produktów, a tym samym do rozwoju społeczeństwa.
Michelin jest jednym z największych na świecie producentów opon – posiada ponad 70 fabryk w 20 krajach. Stale inwestuje w rozwój technologii produkcji, by móc oferować innowacyjne produkty dostosowane do zmieniających się wymogów rynku. Fabryka w Vitorii w północnej części Hiszpanii stanęła przed koniecznością budowy nowego magazynu, przeznaczonego do składowania gumy wykorzystywanej w procesie produkcji opon.
Priorytetową kwestią w przypadku tego obiektu było uzyskanie jak największej pojemności magazynowej poprzez maksymalne wykorzystanie dostępnej powierzchni. Jak wyjaśnia Antonio J. García-Montalvo, odpowiedzialny za kierowanie tym projektem po stronie Michelina: „poprzedni magazyn był mniejszy, więc konieczne było układnie kontenerów w stosy, co nie należało do zbyt praktycznych rozwiązań”.
„Ekipa techniczna Mecaluxu pracowała nad projektem praktycznie przez cały rok 2017, gdyż budowa takiego obiektu wymaga dogłębnej analizy potrzeb” – zauważa Antonio J. García-Montalvo. Przedsięwzięcie obejmowało równocześnie rozbudowę budynków znajdujących się w otoczeniu nowego magazynu. Wymagało to doskonałej koordynacji jednoczesnej pracy ponad 170 specjalistów i zastosowania żurawi o udźwigu 70 ton.
W rezultacie powstał magazyn zintegrowany z fabryką umożliwiający składowanie wszystkich produktów opuszczających linie produkcyjne. Dzięki temu budynek, który poprzednio służył jako magazyn, zmienił swoje przeznaczenie – zamontowano w nim bowiem kolejną linię produkcyjną.
Magazyn pracuje pełną mocą przez 24 godziny na dobę, 7 dni w tygodniu. „Teraz transport gotowych produktów do magazynu i na rampy załadunkowe odbywa się szybciej” – wskazuje Antonio J. García-Montalvo.
Magazyn „szyty na wymiar”
Nowy obiekt o wysokości 27 m to magazyn samonośny. Jego konstrukcję nośną tworzą regały, które przenoszą nie tylko ciężar własny i składowanych ładunków, ale także ścian i dachu, które są do nich zamocowane. Zaletą tego rozwiązania jest to, że optymalnie wykorzystuje powierzchnię dostępną w kompleksie fabrycznym Michelina, umożliwiając składowanie 4590 kontenerów.
Magazyn składa się z 5 korytarzy, wzdłuż których po obu stronach znajdują się regały o pojedynczej głębokości. Jest w pełni zautomatyzowany, dzięki czemu funkcjonuje przy minimalnym udziale człowieka. Przenośniki, układnice, wózki wahadłowe i windy transportują towar na odpowiednie miejsca na regałach, gwarantując przepływ towaru zgodny z wymogami Michelina. Układnice obsługują 240 kontenerów w ciągu godziny (120 przychodzących i 120 wychodzących).
Specyficzną cechą tego magazynu jest to, że nie stosuje się tutaj palet drewnianych ani plastikowych, lecz metalowe kontenery o wymiarach 1100 x 1250 x 1220 mm, które wyposażone są w nogi zamiast płóz. „Zarówno regały, jak i automatyczne urządzenia transportu bliskiego zostały zaprojektowane w oparciu o wymiary i cechy tych jednostek ładunkowych” – wyjaśnia Antonio J. García-Montalvo.
Przenośniki transportujące kontenery z prędkością kontrolowaną 20 m/min to wersja łańcuchowa, natomiast regały wyposażone są w specjalne podpory kontenerów, które umożliwiają stabilne, a więc bezpieczne składowanie ładunków.
Magazyn spełnia rygorystyczne normy jakości w zakresie warunków przechowywania towaru, aby opony wykazywały odpowiednie właściwości, od których przecież zależy bezpieczeństwo jazdy. Dlatego panuje tutaj temperatura kontrolowana 10–27ºC. Obiekt jest również wyposażony w system gaszenia pożarów w postaci tryskaczy rozmieszczonych na regałach, a także w grodzie przeciwpożarowe, które w razie pożaru zamykają się hermetycznie, co zapobiega rozprzestrzenianiu się ognia.
Magazyn zintegrowany z fabryką
Magazyn składa się z dwóch kondygnacji: na dolnej odbywają się przyjęcia, a na górnej wydania towaru. Jak wyjaśnia Antonio J. García-Montalvo: „taki układ pozwala całkowicie wyeliminować problem wzajemnego zakłócania się obu tych procesów”.
Przyjęcia towaru do magazynu
Kontenery trafiają do magazynu z fabryki ustawione jeden na drugim. Za pomocą wózków widłowych operatorzy umieszczają je na dwóch stanowiskach wejściowych. Następnie sztaplarka zdejmuje górny kontener i umieszcza oba ładunki na przenośniku łańcuchowym, który transportuje je dalej, nie wymagając przy tym zastosowania palet jako podstawy.
Przenośniki dostarczają towar do odpowiednich korytarzy, wyznaczonych przez informatyczny system zarządzania magazynem Easy WMS.
Wydania towaru z magazynu
Podwójny wózek wahadłowy odbiera kontenery, które mają opuścić magazyn, i transportuje je do czterech stanowisk wyjściowych. Tutaj również znajdują się sztaplarki, ale w tym przypadku wykonują czynność odwrotną, czyli układają kontenery parami jeden na drugim. W takiej postaci operatorzy ładują je na ciężarówki, co jak zauważa Antonio J. García-Montalvo: „dynamizuje proces wydawania towaru z magazynu i zwiększa jego wydajność”.
Monitorowanie towaru
Do koordynowania ruchu produktów w magazynie służy autorskie oprogramowanie Mecaluxu – Easy WMS – które zostało przystosowane do specyfiki nowego obiektu i sposobu zarządzania towarem. „Easy WMS komunikuje się z BSM, naszym systemem informatycznym, za pomocą interfejsu, który jest rezultatem testów prowadzonych w Mecaluxie, w naszej fabryce w Vitorii oraz w centrali Michelina w Clermont-Ferrand po to, aby zagwarantować idealną synchronizację obu systemów” – wyjaśnia Antonio J. García-Montalvo.
Dzięki Easy WMS Michelin na bieżąco zna dokładną lokalizację każdego produktu od momentu jego przyjęcia do magazynu aż po załadunek na ciężarówkę.
Antonio J. García-Montalvo – Kierownik projektu w fabryce Michelina w Vitorii
„Do realizacji tego magazynu wybraliśmy Mecalux po przeanalizowaniu propozycji jeszcze pięciu innych firm. Przekonało nas doświadczenie Mecaluxu w budowie obiektów samonośnych oraz wysoka jakość produktów i możliwość ich dostosowania do wykorzystywanych przez nas metalowych kontenerów”.
Korzyści dla firmy Michelin:
- Maksymalna wydajność: w pełni automatyczny magazyn samonośny, zintegrowany z fabryką, pracuje 24 godziny na dobę przez 7 dni w tygodniu.
- Magazyn „szyty na wymiar”: obiekt i jego wyposażenie zostały zaprojektowane pod kątem składowania i transportu metalowych kontenerów o wymiarach 1100 x 1250 x 1220 mm.
- Magazyn „pod klucz”: Mecalux zbudował obiekt i wyposażył go nie tylko w regały i urządzenia transportu bliskiego, ale również w oprogramowanie magazynowe, zabezpieczenia oraz systemy chłodzenia i ochrony przeciwpożarowej.
Automatyczny magazyn samonośny Michelin | |
---|---|
Pojemność magazynowa: | 4590 pojemników |
Wymiary kontenera: | 1100 x 1250 x 1220 mm |
Maksymalna waga kontenera: | 850 kg |
Wysokość magazynu: | 27 m |
Długość regałów: | 38 m |
Galeria
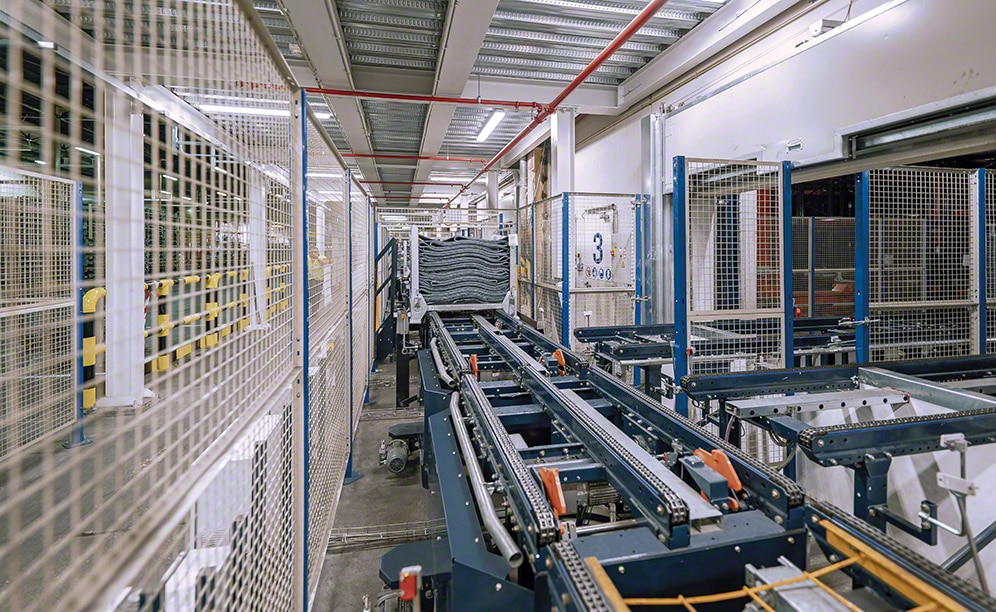
Przenośniki łańcuchowe dostosowane do wymiarów metalowych kontenerów
Zapytaj eksperta