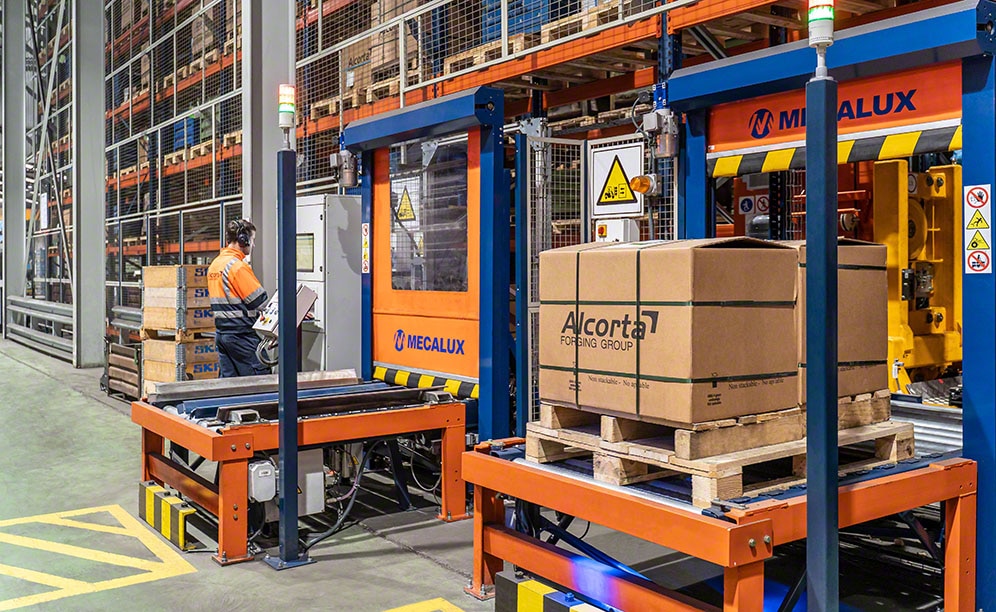
Alcorta Forging Group: technologia łącząca magazyn z produkcją
Alcorta Forging Group uruchomił automatyczny magazyn części samochodowych zarządzany przez Easy WMS
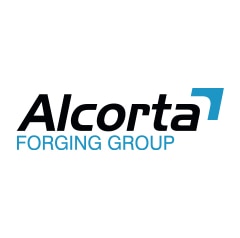
Proces ciągłego doskonalenia jest integralną częścią filozofii działania hiszpańskiego producenta metalowych części samochodowych – Alcorta Forging Group. Przedsiębiorstwo uruchomiło w swoim zakładzie produkcyjnym w Elgóibar w Kraju Basków automatyczny magazyn o wysokości 14 m i pojemności 1115 palet. Obiektem zarządza oprogramowanie magazynowe Easy WMS Mecaluxu, zapewniając prawidłowy i bezpieczny przepływ ok. 300 przychodzących i wychodzących palet z surowcami i produktami gotowymi.
Wykuwanie rozwiązań
Alcorta Forging Group to działająca w branży metalurgicznej firma o ponad stuletniej tradycji. Jej siedziba mieści się w Elgóibar w Kraju Basków, ale firma prowadzi działalność również w Niemczech, Francji, Czechach, Republice Południowej Afryki, Chinach i Stanach Zjednoczonych.
Jej początki sięgają 1911 roku, kiedy to Teodoro Alcorta i Esteban Unzueta założyli spółkę i zaczęli produkować ręczną broń palną. W latach 80. firma przestawiła się na produkcję części dla branży motoryzacyjnej. Jej najważniejszymi wartościami są: ciągły rozwój, wysoka jakość i innowacyjność produktów oraz poszanowanie środowiska naturalnego.
Obroty Alcorta Forging Group sięgają ponad 70 milionów euro rocznie, z czego 85% pochodzi z eksportu, głównie do Francji, Niemiec i RPA. Obecnie firma jest jednym z największych przedsiębiorstw metalurgicznych w Hiszpanii.
Silnik zakładu produkcyjnego
Każdego roku fabryka w Elgóibar produkuje ok. 20 milionów części, które są montowane w samochodach najbardziej znanych marek, takich jak m.in. Audi, BMW, Lamborghini, Ferrari, Volvo i Volkswagen. Dla Alcorta Forging Group priorytetem jest zadowolenie klientów, dlatego nieustannie opracowuje nowe rozwiązania, by skutecznie odpowiadać na potrzeby coraz bardziej wymagającego rynku.
José Antonio Fernández, Kierownik Magazynu w Elgóibar, podkreśla, że firma stale ulepsza i modyfikuje procesy, aby zapewnić ich maksymalną wydajność: „Obecnie notujemy bezprecedensowy wzrost. Aby być w stanie obsłużyć zwiększającą się liczbę odbiorców, wkładamy sporo wysiłku w ulepszanie i automatyzację wszystkich procesów, w tym także logistyki”.
Zgodnie z tym założeniem Alcorta Forging Group uruchomiła automatyczny magazyn połączony z zakładem produkcyjnym. Komunikacja pomiędzy obszarami odbywa się w obu kierunkach. Zadaniem magazynu jest zaopatrywanie linii produkcyjnych w surowce i odbiór gotowych produktów.
Jak wyjaśnia José Antonio Fernández: „celem przedsięwzięcia było uzyskanie możliwości dokładnego monitorowania całego procesu logistycznego – od momentu przyjęcia surowców do magazynu po wysyłkę gotowych produktów do odbiorców”. Wdrożenie oprogramowania magazynowego Easy WMS firmy Mecalux scentralizowało wszystkie informacje o produktach i monitoruje ich obieg w magazynie, gwarantując tym samym ich pełną identyfikowalność.
Projekt magazynu „wykorzystuje wysokość budynku w celu uzyskania większej pojemności” – dodaje José Antonio Fernández. Magazyn o wysokości 13 m i długości 54 m składa się z dwóch korytarzy z zamontowanymi po obu stronach regałami o pojedynczej głębokości. Umożliwiają one składowanie 1115 palet z ponad 300 różnymi pozycjami asortymentowymi.
Magazyn automatyczny
Magazyn podzielony jest na dwa obszary robocze:
- Frontowa część regałów, połączona z produkcją: strefa wydań surowców na produkcję oraz strefa przyjęć produktów z fabryki;
- Bok magazynu skomunikowany z rampami załadunkowo-rozładunkowymi: strefa przyjęć surowców od dostawców i z innych fabryk firmy oraz strefa wydań gotowych produktów wysyłanych do odbiorców finalnych.
Każdego dnia do magazynu przyjmowanych jest 150 palet zarówno od dostawców, jak i z linii produkcyjnych. Wszystkie muszą przejść przez stanowisko kontrolne, gdzie są sprawdzane pod kątem spełniania obowiązujących w magazynie wymogów w zakresie m.in. wagi i wymiarów.
Następnie Easy WMS wyznacza miejsca składowania, osobno dla surowców i dla gotowych produktów, uwzględniając również szybkość rotacji. „Dzięki tej metodzie pracy zoptymalizowaliśmy wykorzystanie zasobów w zapewnianiu kontroli nad stanem magazynowym” – zauważa José Antonio Fernández.
Odpowiednie rozmieszczenie ładunków w magazynie ma ogromny wpływ na przebieg procesu logistycznego, ponieważ, jak mówi kierownik magazynu: „przyspiesza i usprawnia wykonywanie wszelkich operacji, a zwłaszcza przygotowywanie zamówień”.
Ponadto dzięki Easy WMS znana jest dokładna lokalizacja każdego ładunku. Pełna identyfikowalność stanu magazynowego znacznie redukuje ryzyko pomyłek i błędów oraz niedostępności towaru.
Easy WMS jest zintegrowany z systemem zarządzania zasobami przedsiębiorstwa (ERP) stosowanym przez firmę Alcorta Forging Group. W celu zwiększenia efektywności procesu logistycznego systemy te stale się ze sobą komunikują i wymieniają dane w obu kierunkach.
W każdym korytarzu pracuje układnica dwukolumnowa, która transportuje przyjęte do magazynu palety na miejsca składowania wyznaczone przez WMS. Te automatyczne urządzenia poruszające się z prędkością 120 m/min w poziomie znacznie usprawniają procesy związane ze składowaniem, kompletacją i wysyłką ładunków.
Magazyn opuszcza codziennie 150 palet, a więc tyle samo, ile jest przyjmowanych. Zawierają one zarówno surowce, jak i produkty gotowe. Pierwsze trafiają na produkcję, drugie zaś są wysyłane do odbiorców. Palety opuszczają magazyn sekwencyjnie. Ładunki oczekujące na załadunek na ciężarówki są pogrupowane według zamówień lub tras.
Zalety magazynu automatycznego
- Wydajność i dostępność. Magazyn może pracować na pełnych obrotach nieprzerwanie przez całą dobę.
- Niższe koszty eksploatacji. Dzięki automatyzacji czynności magazynowych do obsługi towaru ładunków wymagana jest mniejsza liczba pracowników.
- Ciągła inwentaryzacja. System zarządzania identyfikuje i monitoruje stan magazynowy w czasie rzeczywistym.
- Maksymalna pojemność magazynowa. Regały optymalizują wykorzystanie miejsca dostępnego w magazynie.
Integracja i automatyzacja
Automatyzacja logistyki zapewnia firmie Alcorta Forging Group ciągły przepływ ładunków, zwiększając jej zdolność produkcyjną, minimalizując ryzyko błędów i obniżając koszty. Nowy magazyn jest zintegrowany z fabryką, by zaopatrywać ją w surowce niezbędne do wyprodukowania ok. 20 milionów części rocznie, a następnie odbierać gotowe produkty, aby na czas trafiły do odbiorców.
Nowoczesna technologia jest łącznikiem między produkcją i logistyką. Układnice i przenośniki paletowe usprawniają procesy przyjęcia i wysyłki ładunków, a system zarządzania magazynem zapewnia pełną identyfikowalność produktów. Dzięki rozwiązaniom zaproponowanym przez Mecalux firma Alcorta Forging Group nadal może rozwijać się zgodnie z wyznawaną filozofią – procesem ciągłego doskonalenia.
José Antonio Fernández – Kierownik Magazynu firmy Alcorta Forging Group w Elgóibar
„Magazyn doskonale spełnia zadanie, do którego został zaprojektowany: integruje logistykę z procesem produkcyjnym. Dzięki automatyzacji mogliśmy zoptymalizować kontrolę nad stanem magazynowym oraz przygotowywanie zamówień”.
Korzyści dla firmy Alcorta Forging Group
- Pełna identyfikowalność: Easy WMS umożliwia identyfikację pochodzenia, a następnie śledzenie produktu na każdym etapie procesu produkcyjnego.
- Magazyn zintegrowany z produkcją: magazyn zaopatruje fabrykę w surowce oraz odbiera z niej i wysyła 150 palet z gotowymi produktami.
- Optymalne wykorzystanie przestrzeni: regały o długości 54 m i wysokości 13 m wykorzystują zarówno powierzchnię, jak i wysokość magazynu, maksymalizując jego pojemność.
Magazyn firmy Alcorta Forging Group | |
---|---|
Pojemność magazynowa: | 1115 palet |
Wymiary palety: | 800 / 1000 x 1200 mm |
Maksymalna waga palety: | 1300 kg |
Wysokość regałów: | 13 m |
Długość regałów: | 54 m |
Galeria
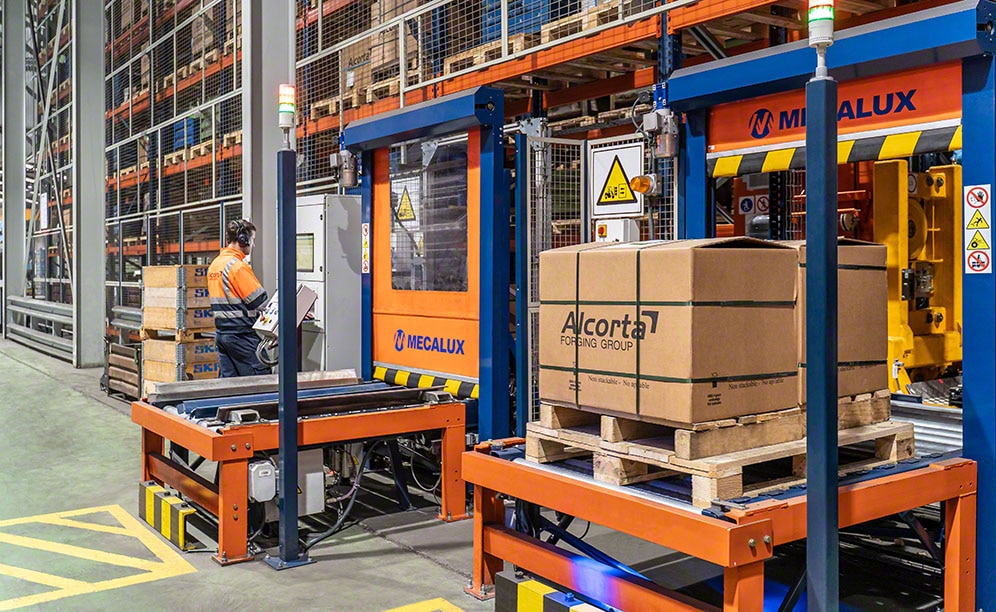
Automatyczny magazyn częśći samochodowych firmy Alcorta Forging Grpup
Zapytaj eksperta