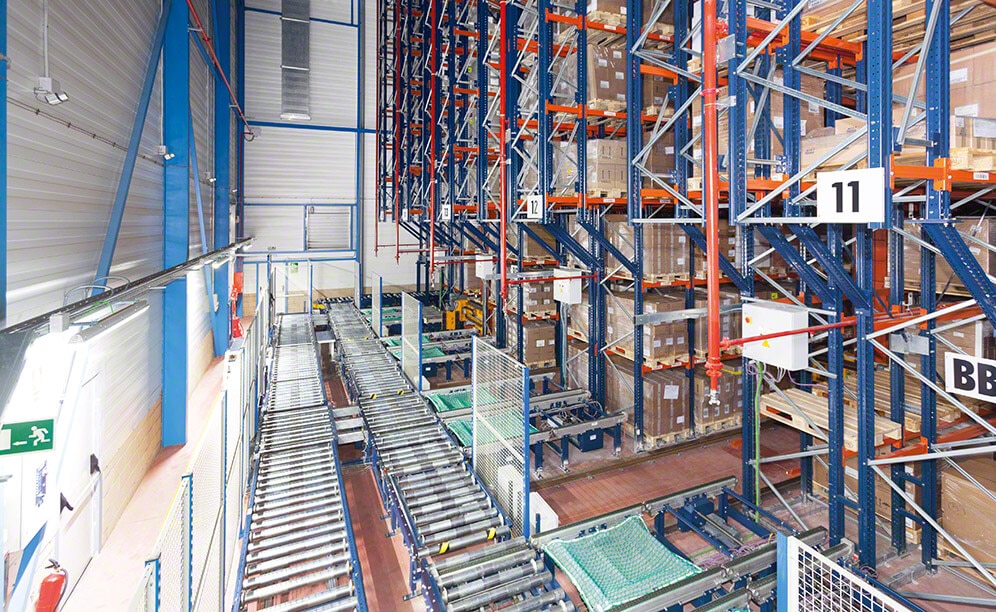
Disalfarm zwiększa pojemność, wydajność i kontrolę dzięki automatyzacji magazynu
Dzięki zastosowaniu układnic trójstronnych Disalfarm w prosty i ekonomiczny sposób automatyzuje swój magazyn
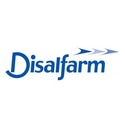
W Rubí nieopodal Barcelony, na powierzchni 39 027 m2, wybudowane zostało centrum logistyczne Disalfarm. Ten magazyn automatyczny, mieszczący obecnie ponad 19 000 palet, znacznie poprawił wydajność firmy. Modernizacja i rozbudowa przeprowadzone zostały w trakcie funkcjonowania obiektu bez konieczności jakichkolwiek przestojów na czas wykonywania prac.
O firmie Disalfarm
Disalfarm S.A. to firma logistyczna, którą w Hiszpanii założyły koncerny farmaceutyczne Bayer, Boehringer Ingelheim i Novartis, aby skupić w jednym miejscu odbywające się na tamtejszym rynku procesy składowania i dystrybucji produkowanych przez siebie farmaceutyków.
Spółka rozpoczęła działalność w 2000 roku i zgodnie z wizją jej założycieli miała stać się liderem w branży dystrybucji leków. Aby osiągnąć ten cel, niezbędne było wdrożenie systemu jakości gwarantującego spełnianie norm w zakresie produkcji i dystrybucji określonych w obowiązujących przepisach.
Bogata oferta produktów leczniczych, których dystrybucją zajmuje się Disalfarm, zawiera między innymi leki dostępne na receptę, leki do użytku szpitalnego, suplementy diet i leki weterynaryjne.
Lokalizacja centrum dystrybucyjnego
Centrum logistyczne Disalfarm S.A. zlokalizowane jest w podbarcelońskiej miejscowości Rubí, w strefie przemysłowej usytuowanej przy ważnym węźle komunikacyjnym. Obiekt sąsiaduje z głównymi centrami logistycznymi i dystrybucyjnymi, co pozwala zaoferować sprawną i szybką obsługę wszystkim klientom.
Modernizacja bez zakłócania pracy obiektu
W ostatnich latach Disalfarm odnotował wzrost, który spowodował, że jego potrzeby magazynowe uległy istotnym zmianom w stosunku do sytuacji z 2000 roku. Powstałe wówczas centrum logistyczne przeznaczone było zarówno do składowania produktów, jak i do przygotowywania zamówień, spośród których mniej niż 20% dotyczyło pełnych palet z jedną pozycją asortymentową.
W tym etapie powstały jeszcze dwie hale magazynowe, strefa kompletacji i konsolidacji zamówień, rampy załadunkowo-rozładunkowe oraz część biurowa z zapleczem socjalnym. Łączna powierzchnia obiektów wynosiła 9706 m2. Wszystkie regały w magazynie i strefę kompletacji wykonał Mecalux.
W 2007 roku część magazynowa okazała się zbyt mała. Ponadto panował tu tak nasilony ruch wózków widłowych, że generowane koszty były niewspółmiernie wysokie, a jednocześnie powodował on duże ryzyko wypadków przy pracy, co zgodnie ze standardami Disalfarmu było absolutnie niedopuszczalne.
W obliczu tej sytuacji Disalfarm zlecił Mecaluxowi modernizację swojego centrum logistycznego, przy czym wyzwaniem było przeprowadzenie prac w taki sposób, aby nie zakłócić codziennej działalności obiektu, gdyż mogliby na tym ucierpieć odbiorcy Disalfarmu.
Etap 1. i etap 2. – punkt wyjścia
W pierwszym etapie, który miał miejsce w 2000 roku, powstały następujące części centrum logistycznego:
- Magazyn dla 12 900 palet o wymiarach 800 x 1200 mm składający się z 10 korytarzy z regałami o wysokości 15 m.
- Strefa kompletacji wyposażona w regały przepływowe z systemem pick-to-light i przenośniki do transportu kartonów, które łączą ją ze strefą konsolidacji i pakowania.
- Strefa kompletacji pełnych kartonów bezpośrednio z palet.
- Magazyn do składowania produktów wymagających niskiej temperatury mieszczący 290 palet.
- Magazyn z ograniczonym dostępem przeznaczony do składowania leków psychotropowych.
- Dziewięć ramp załadunkowo-rozładunkowych z obszernym placem manewrowym.
W drugim etapie zostało dodanych pięć korytarzy z regałami paletowymi mieszczącymi 6450 palet, co dało łączną pojemność magazynową wynoszącą 19 350 palet. Ponadto powstały wówczas trzy nowe rampy.
Przepływ towarów również znacząco się zwiększył i wynosił 1100 palet dziennie (500 wchodzących i 600 wychodzących). Aby możliwa była obsługa tylu palet, wykorzystywano następujące zasoby:
- Siedem wózków czołowych – obsługa ramp, dostarczanie towaru do stref kompletacji oraz układanie i pobieranie palet przed korytarzami.
- Pięć wózków trójstronnych – wyłącznie obsługa korytarzy.
- 24 operatorów do obsługi wózków (12 na każdej zmianie).
Przepływ towarów w magazynie powstałym w etapach 1. i 2.
Towar przychodził do magazynu na paletach. Operator odczytywał kod kreskowy każdej palety za pomocą terminala, a system zarządzania magazynem wskazywał mu odpowiedni korytarz i miejsce składowania. Następnie paleta była transportowana za pomocą wózka czołowego do miejsca odkładczego u wejścia do korytarza, skąd wózek trójstronny przenosił ją do wyznaczonego miejsca na regale.
Proces wydawania towaru obejmował te same czynności, ale wykonywane w odwrotnej kolejności, przy czym większość palet kierowana była do stref kompletacji.
Etap 3. – likwidacja transportu wewnętrznego pełnych palet
Rozwój firmy nie wymagał zwiększenia liczby miejsc składowania, lecz większego przepływu palet. Aby sprostać tej potrzebie, rozważano możliwość zwiększenia liczby wózków i operatorów, ale wiązało się to z większym ryzykiem wypadków.
Obiekt składał się z 15 korytarzy obsługiwanych przez pięć wózków trójstronnych. Chociaż możliwe było dodanie pięciu wózków, odrzucono takie rozwiązanie, ponieważ są to urządzenia półautomatyczne i niezbyt szybkie, a liczba cykli, jakie przy ich wykorzystaniu można było osiągnąć, okazała się niewystarczająca, aby zaspokoić potrzeby Disalfarmu.
Wówczas Mecalux zaproponował dwie możliwości polegające na zastosowaniu przenośników rolkowych i łańcuchowych, aby wyeliminować konieczność korzystania z wózków z przeciwwagą wewnątrz magazynu.
Pierwsza propozycja etapu 3. – odrzucona
W projekcie zaproponowano strefę przednią składającą się z następujących elementów:
- Dwa główne odgałęzienia prostopadłe do regałów.
- Dwa przenośniki (wejściowy i wyjściowy) w każdym korytarzu.
- Stanowisko wejściowe w strefie ramp z kontrolą palet i miejscem na odrzucone palety.
- Bezpośrednie wyjście do strefy wysyłki.
- Dwa wyjścia do stref kompletacji.
Ta opcja zapewniała bliskość ramp, a także sprawne zaopatrywanie stanowisk kompletacyjnych.
Składowanie miało się odbywać z użyciem wózków trójstronnych. Wersja ta zakładała, że w przyszłości zostanie zwiększona liczba wózków lub zostaną zastosowane urządzenia automatyczne. Ponadto w tylnej części obiektu wózki trójstronne miały zmieniać korytarze, tak jak to się odbywało w magazynie z etapu pierwszego.
Druga propozycja etapu 3. – przyjęta
Zdecydowano, że główna część strefy przedniej znajdzie się w tylnej części magazynu. W ten sposób, tak jak dotychczas, korytarz główny miał służyć do wykonywania manewrów zmiany korytarzy przez wózki trójstronne i do przemieszczania się wózków czołowych.
Realizacja tego rozwiązania była bardziej złożona i droższa, ponieważ zakładało ono zamontowanie przenośnika w dolnej części jednego z regałów, aby zapewnić transport towarów z ramp. To samo dotyczyło towarów wychodzących. Jednakże było to jedyne rozwiązanie, które można było wdrożyć bez zakłócania codziennej pracy magazynu.
Przemieszczanie towarów między przenośnikami wejściowymi i miejscami składowania odbywało się za pomocą wózków trójstronnych. Kiedy przebudowa została ukończona, główny korytarz był dostępny jedynie do zmiany korytarzy przez wózki trójstronne i do bezpośrednich wydań do strefy wysyłki, które były w tym magazynie niezbyt liczne.
Wówczas wdrożono także moduł sterujący Galileo, który stał się odpowiedzialny za zarządzanie automatyczną pracą przenośników, począwszy od strefy przyjęć, przez strefę kompletacji, po strefę wydań. Terminale radiowe pozostały w użytku, aby wskazywać operatorom wózków trójstronnych, dokąd lub skąd mają zabierać poszczególne palety.
Etap 4. – pełna automatyzacja magazynu
Automatyzacja przyjęć i wydań towarów sprawdziła się doskonale, dlatego wobec perspektywy wzrostu pojawił się pomysł zautomatyzowania całego magazynu.
Pełna automatyzacja niosła ze sobą kolejną niedogodność – układnice dostępne na rynku nie umożliwiają układania palet na poziomie posadzki, więc jedynym sposobem na poradzenie sobie z tym problemem jest podniesienie pierwszego poziomu regałów na wysokość 60–70 cm od posadzki oraz umieszczenie prowadnicy w górnej części korytarzy. Takie rozwiązanie skutkowałoby jednak utratą całego poziomu ładunkowego, co oznaczałoby zmniejszenie pojemności magazynowej o 1290 palet.
Disalfarm nie mógł sobie pozwolić na redukcję pojemności magazynowej, dlatego konieczne było znalezienie innego sposobu na automatyzację albo wybudowanie nowego centrum logistycznego.
W tym czasie Mecalux wprowadził na rynek układnicę trójstronną, będącą w pełni automatyczną alternatywą dla wózka trójstronnego. Taka układnica idealnie nadawała się do zastosowania w centrum logistycznym Disalfarmu. Urządzenie to ma następujące cechy:
- Może układać palety na wysokości zaledwie 10 cm od posadzki.
- Wyposażone jest w widły trójstronne zamiast bocznych wideł teleskopowych.
- Nie posiada górnego zespołu prowadzącego, zatem wymaga tylko dwóch prowadnic na posadzce.
- Jego maksymalna wysokość to 15 m.
- Może wykorzystywać most transferowy (zmiana korytarza).
- Jest sterowane za pomocą modułu Galileo.
- Ma co najmniej taką samą ładowność jak wózki trójstronne.
Zmiany wprowadzone w etapie 4.
Zmiany, jakie zostały wprowadzone w tym etapie budowy magazynu, były nieznaczne i łatwe w realizacji. Polegały one główne na:
- Zamontowaniu dwóch prowadnic na posadzce.
- Nieznacznym zmodyfikowaniu odległości między poziomami.
- Przedłużeniu stanowiska kontrolnego na przenośnikach strefy przedniej,
- Zamontowaniu ogrodzenia zabezpieczającego zgodnie z przepisami dotyczącymi automatyzacji magazynów, zwłaszcza w zakresie bezpieczeństwa w korytarzach obsługiwanych przez układnice.
Dostęp do korytarzy w celu przeprowadzenia czynności serwisowych znajduje się po przeciwnej stronie względem strefy przedniej, to znaczy tam, gdzie znajdował się korytarz główny, gdy magazyn obsługiwany był przez wózki trójstronne.
Z magazynu wysyłanych jest niewiele pełnych palet. Wzdłuż korytarza z miejscami odkładczymi, które istniały w pierwotnej strefie przedniej, utworzono dla nich kanał przepływowy. Dostęp do niego odbywa się za pomocą wózków z przeciwwagą, bez konieczności wjeżdżania do stref zautomatyzowanych.
Oprogramowanie magazynowe
Od samego początku istnienia centrum logistyczne Disalfarm posiada rozbudowany system zarządzania magazynem dostosowany do jego potrzeb. Możliwość dalszego wykorzystywania tego oprogramowania jako narzędzia kierującego pracą całego magazynu była warunkiem koniecznym.
Z tego względu potrzebne było tylko wdrożenie standardowego programu sterującego Mecaluxu – Galileo Control System. Kieruje on wszystkimi urządzeniami automatycznymi, które pracują w magazynie. Ponadto opracowany został interfejs komunikacyjny, aby zapewnić prawidłową wymianę danych między obydwoma systemami, a także warstwę pośrednią, aby zapobiec niespójnym poleceniom.
Korzyści dla Klienta:
- Duża pojemność magazynowa na ograniczonej powierzchni: magazyn może pomieścić 19 350 palet o wymiarach 800 x 1200 mm.
- Modernizacja bez konieczności przestojów w pracy magazynu: Mecalux zoptymalizował funkcjonowanie centrum logistycznego Klienta bez konieczności wstrzymywania funkcjonowania obiektu.
- Wysoka wydajność: automatyzacja procesu składowania umożliwiła zwiększenie przepływu towarów zgodnie z potrzebami Klienta.
- Pełna kontrola: interfejs komunikacyjny łączący system zarządzania magazynem i program sterujący pozwalają zarządzać wszystkimi procesami i czynnościami odbywającymi się w magazynie.
Magazyn Disalfarm w Barcelonie | |
---|---|
Pojemność magazynowa: | 19 350 palet |
Wymiary palety: | 800 x 1200 mm |
Maksymalna waga palety: | 800 kg |
Wysokość regałów: | 13 m |
Długość regałów: | 60 m |
Liczba układnic: | 15 |
Typ układnicy: | automatyczna układnica trójstronna |
Galeria
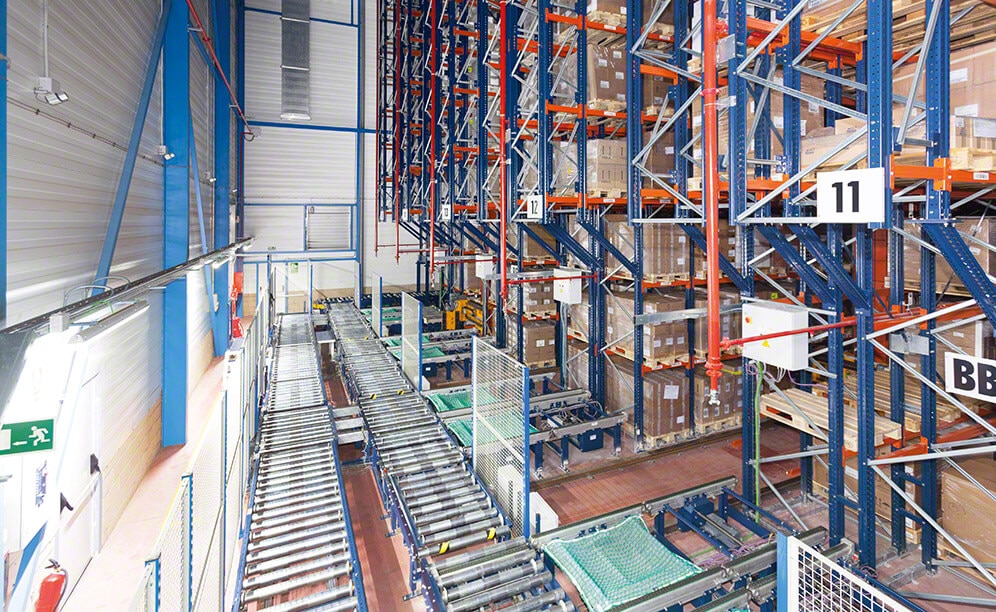
The warehouse, now fully automated and with a storage capacity for more than 19,000 pallets, has significantly improved the productivity of the company
Zapytaj eksperta